Brunswick VIC
Australia
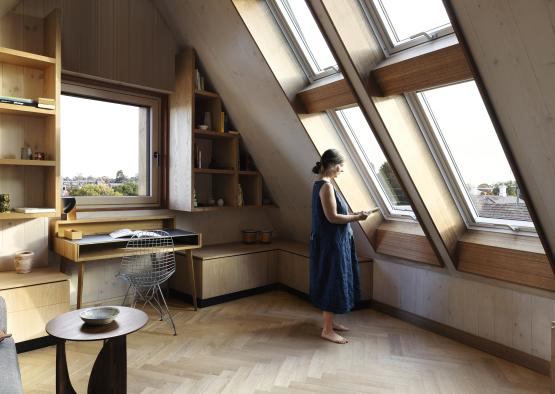
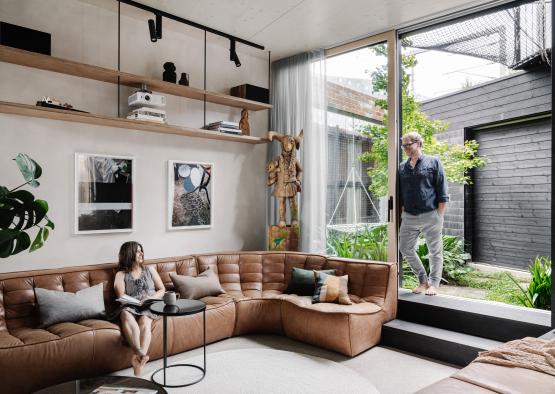
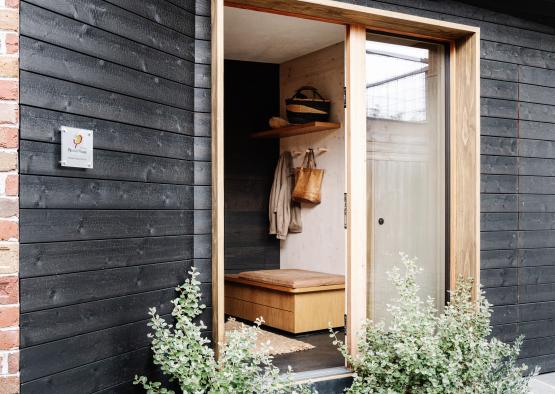
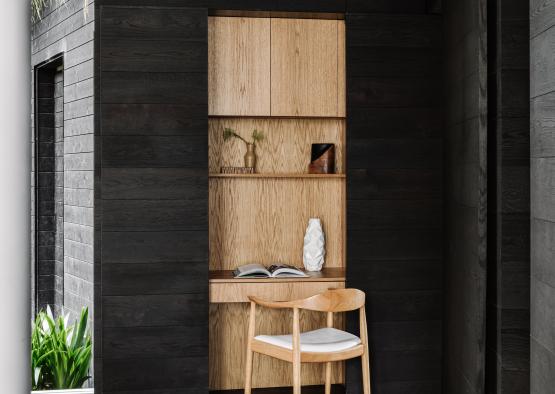

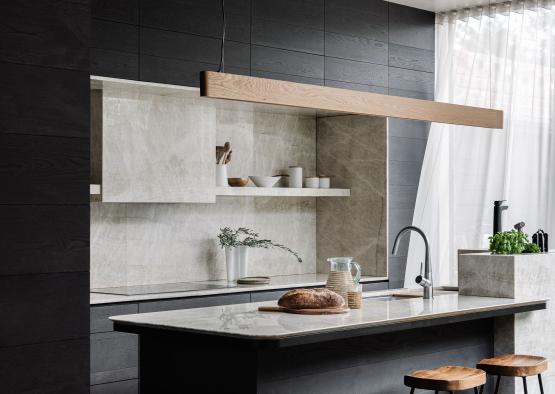
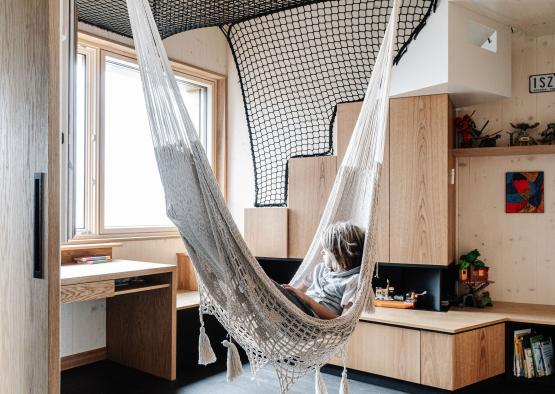
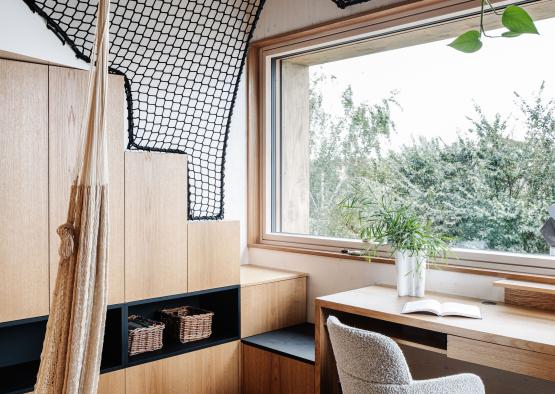
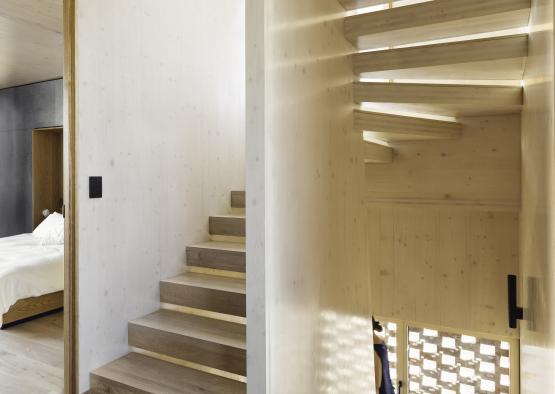
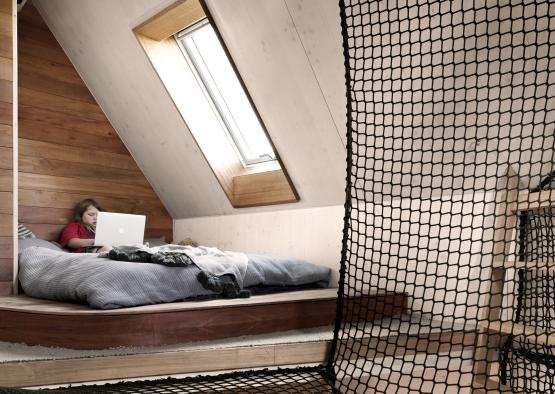
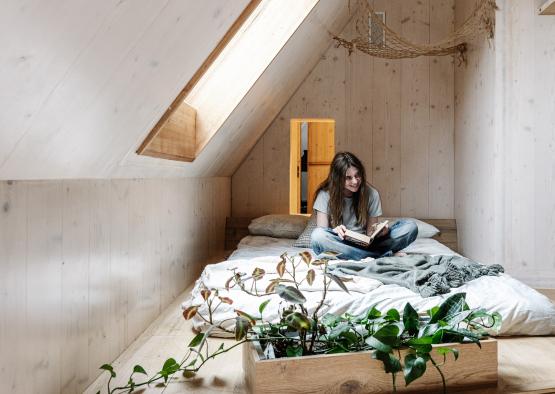
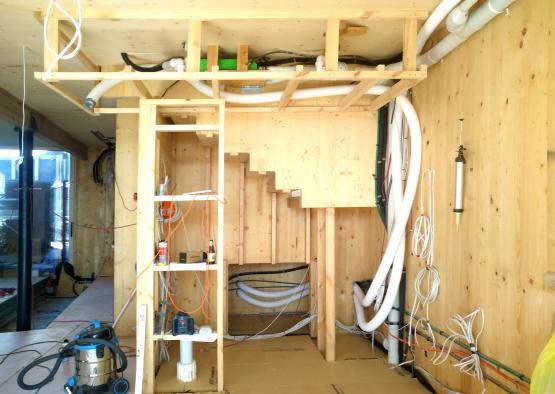
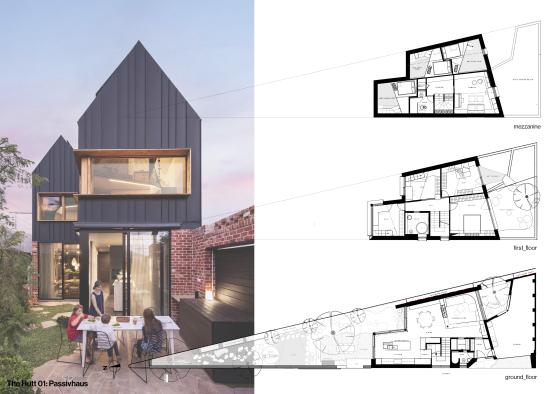
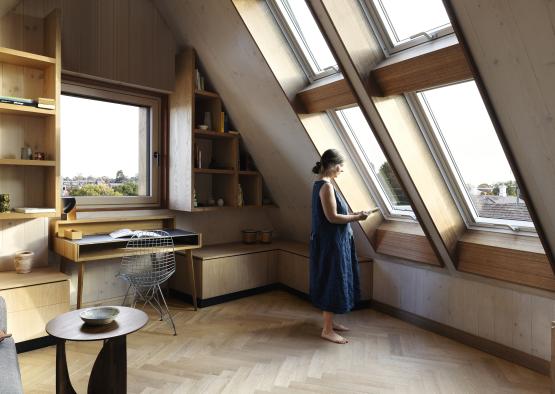
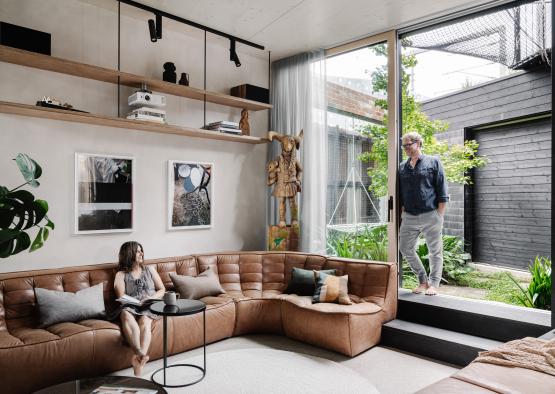
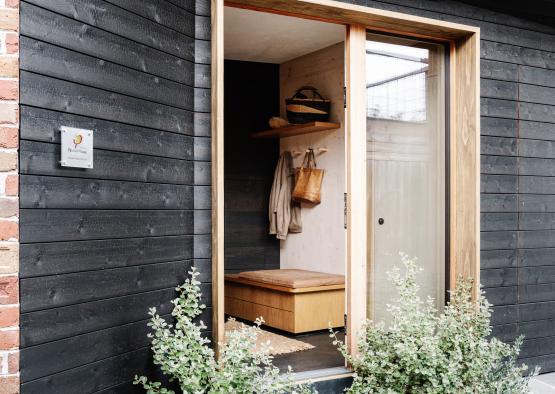
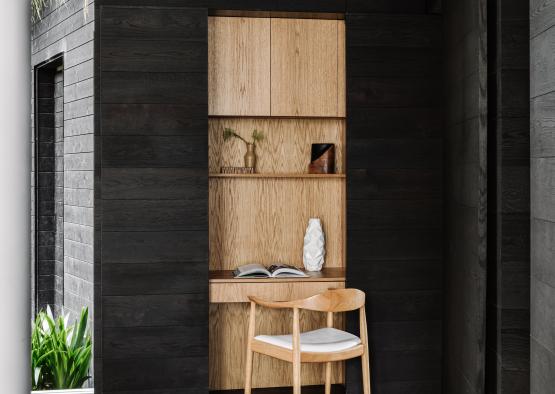
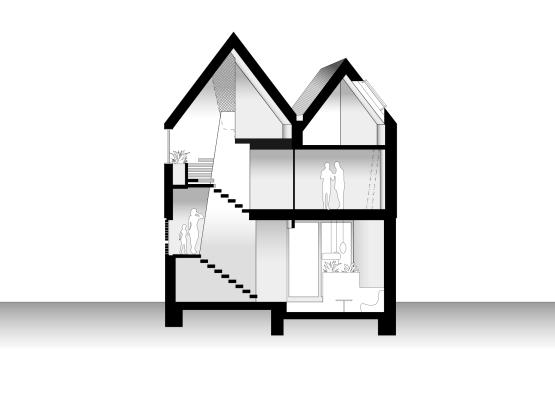

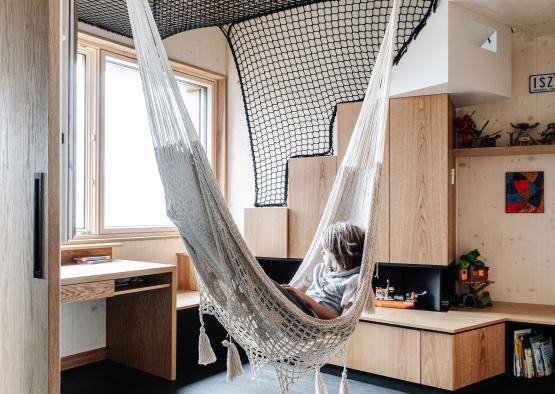
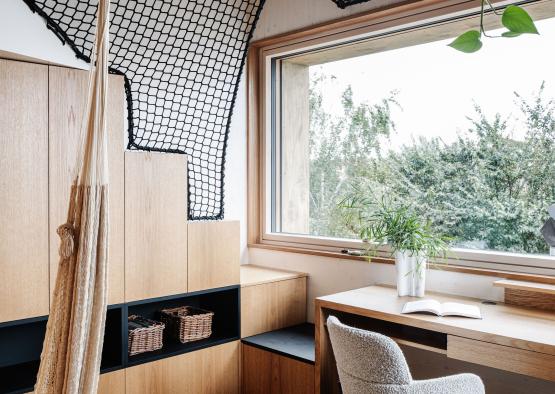
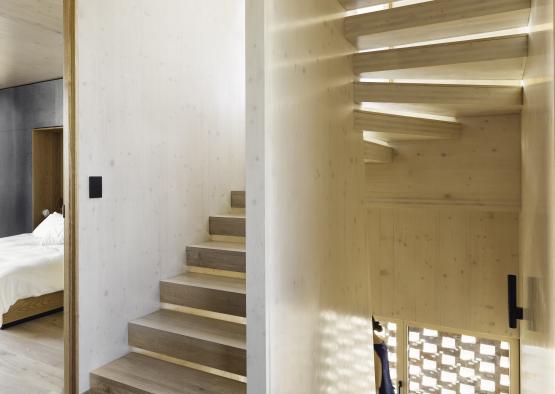
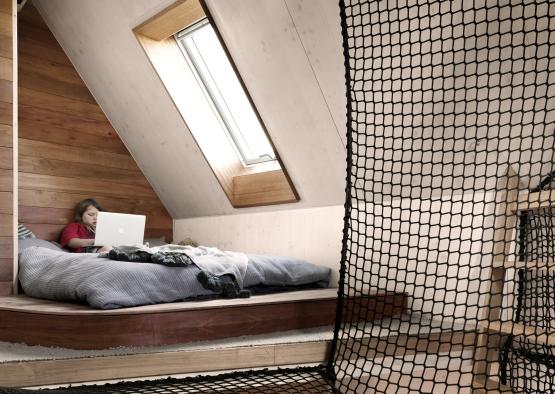
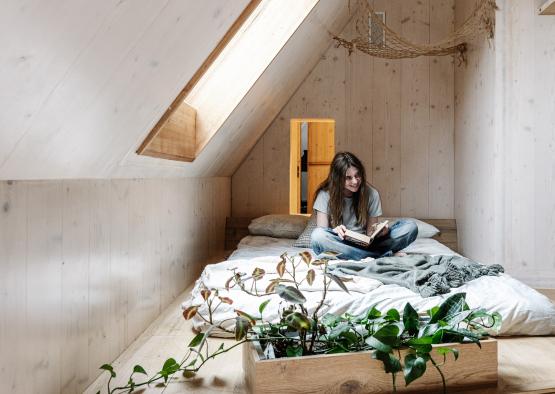
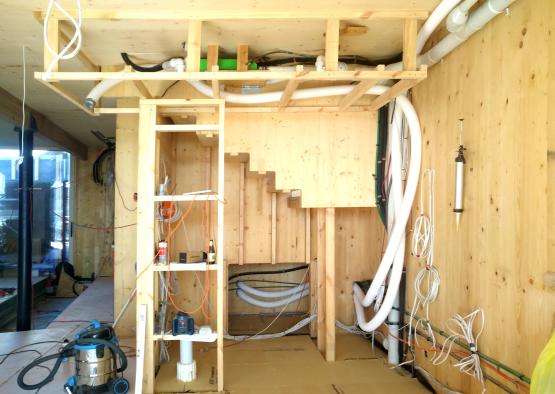
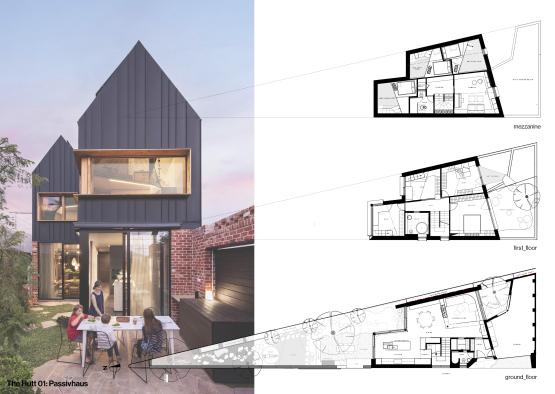
Overview
Hutt 01 has been designed to showcase the way forward for Australian sustainable living. It exemplifies how a sustainable design approach and Passivhaus construction principles can result in a modern luxury lifestyle home. Passivhaus is a stringent building standard from Europe that combines airtightness, heat recovery ventilation, and high insulation values to achieve very stable internal temperatures.
See a WoodSolutions seminar video presentation of this award-winning project at https://youtu.be/1B4zlwSoNVc
-37.7670374, 144.9621035
Structure
Hutt 01 is constructed from a prefabricated Cross-Laminated-Timber (CLT) structure. CLT is a modern form of timber construction, within the emerging area of mass timber construction, which is increasingly being used as a concrete substitute. CLT not only makes the building score better than carbon zero in terms of embedded energy, but also provides a beautiful biophilic interior inherent in the material. CLT is excellent for passive house construction. For Hutt 01, the CLT is complemented with continuous wood fibre insulation, preventing thermal bridging, which allows heat to transfer through conductive materials. The insulating building materials create a high-performance building envelope. The higher mass and density (compared to traditional lightweight construction/insulation) also provides much increased summer performance and acoustics, almost completely blocking out the noise from the adjacent train line.
All structural elements of this building are made from engineered timber (CLT & Glulam), expect for the concrete slab on ground (which is Boral’s Envisia with 70% cement replacement). The slab provides a strong foundation to support the CLT, and acts as thermal mass to assist with temperature regulation.
CLT has been used for both external and internal walls, ceilings, mezzanines , all roofs (including the garage flat roof), and even the staircases. All three levels contain a central glulam beam, allowing efficient spans for supporting the mass timber elements. Ceilings and roofs, as well as the majority of walls, have mostly been left exposed with a warm whitewash finish.
Utilising mass timber prefabricated methodology was one of the key considerations in taking this project beyond carbon zero to actually sequestering carbon within the building. It not only means substantial reduction in carbon footprint and embodied energy, but also a reduction of other, less sustainable finishing materials and trades like plastering from the project. 90% of all internal surfaces are natural materials - mostly timber in raw and finished forms, balanced off with some natural stone and clay render - adding to the inherent biophilic and health aspects of the project. Cutting down on the breadth of trades also meant significant cost savings.
Prefabrication further helped to minimise wastage by optimising panel cuts prior to manufacturing. Offcuts and leftover pieces that would have just gone to waste on site, were utilised to create transport sledges for the CLT, which the architects then carefully de-assembled after transport, and re-used for a suspended ceiling in the hallway to house HRV ducting.
The thermal-bridge free CLT timber structure was then wrapped in a consistent layer of 140mm natural wood fibre insulation. This is made from compressed wood chips, a natural product, with minimal carbon footprint and great hygrothermal properties, allowing the walls to ‘breathe’ due to its permeability. This minimises condensation risk, while also offering more acoustic/thermal mass than traditional insulation would.
Exterior
The external timber cladding consists of two different profiles/types. Both are horizontally laid pine boards and are visually similar, appearing as charred timber. The main board, however, is a thermally treated, stained, and embossed board called ’Thermowood’, nominally 130mm wide, with an excellent life-expectancy. A smaller, second area has been clad with standard boards charred on site, and finished with stained oil over, to enable a longterm comparison between the two. The thermowood is fully pre-finished, so has not been re-treated on site. The site-charred boards have been finished with a Woca treatment oil.
The three dominant traditional materials in the local neighbourhood are timber, metal and bricks. The home features a modern intepretation of these, a composition that allows it to sit well in the neighbourhood, while at the same time demonstrating its contemporary character. The charred black horizontal timber boards are a reflection of the traditional horizontal weatherboards.
Recycled timbers have been used where possible (e.g. ironbark on the deck, recycled cherry and others for one of the kids beds and internal wall cladding). On the facades, Thermowood, Accoya and charred timbers have been specified as natural materials with enhanced durability, reducing waste and embodied energy in otherwise necessary replacements down the track. The engineered oak boards with black satin oil finish on internal floors and walls are cradle-to-cradle (Silver) certified. All timbers have low VOC finishes (Woca and Osmo Polywax or similar)
Interior
Whitewashed timber surfaces contrast with honey-coloured veneers, while engineered black timber boards line floors and walls. The theme of natural materials is complemented by an integral connection with nature throughout the home.
This home is created with highly sustainable interiors, featuring many different timber surfaces. It combines a contemporary feel with aspects of retro / mid-century modernism and Scandinavian, Japanese and German design influences.
Biophilic design is at the core of this home, always prioritising intimate connection with the outdoors. Low VOC finishes and low emission boards help maintain excellent indoor air quality, aided by the mechanical heat recovery system and the indoor plants. It’s a feel-good home, a healthy home exuding joy. Mezzanines created by exposed CLT floors and roofs provide built-in beds made from recycled timbers on site, and large cargo nets span over the voids to create unexpected spaces for inhabiting.
The CLT panels were ordered in three different gradings according to their level of exposure within the space. In an unexpected flair of drama, a fire on site during construction damaged some of the CLT, but due to it’s high performance in fire situation, the panels were able to be sanded back and used again as planned- a testament to the performance of the material.
Timber floors have been used throughout the house, as they have a minimal carbon footprint, and are integral to the biophilic design aspect of the house. Timber floors are warm, they are welcoming, and they make the house a home. The softness is nice under your feet, and it’s nice to touch. An added benefit is that they can be re-finished over time, rather than having to be replaced. The colours could even be changed down the track when refinishing- an important factor for the designers. Visually, the boards continue from the floor up the walls, before extending out to the external charred timber boards, blurring the boundaries between indoor and out.
The chocolate coloured timber boards wrap from the floors into kitchen joinery, sculpting functional elements and concealing doors as they continue from the floors up the walls, before merging with the charred timber cladding boards in the distance. Arriving on the first floor, the black boards are slowly replaced with lighter colours, aiding a transition into the more tranquil private spaces of the home. On the very top, in the attic, a chevron floor in a very light grey oak enhances creates a new mood altogether. The three timber types play together beautifully and promote the idea of the house becoming both lighter and more private as you go up. The three main timber finishes include the whitewashed CLT, the honey coloured Oak, and the black timber boards. The varied timber palette ensures an interesting, warm and calming colour scheme.