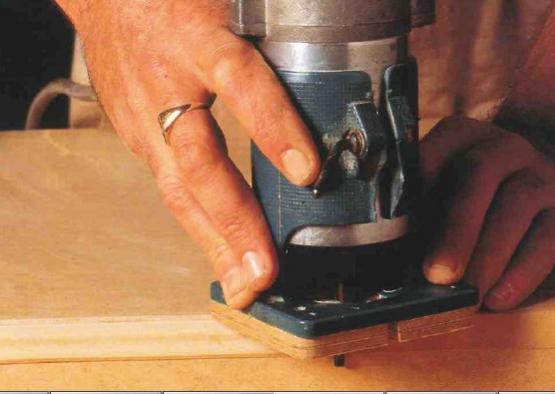
Medium Density Fibreboard (MDF) is a reconstituted wood panel product. It is a dry-processed fibreboard manufactured from wood fibres, as opposed to veneers or particles, and is denser than plywood and particleboard. MDF has an even density throughout and is smooth on both sides.
MDF is reconstituted into wood sheets in a variety of widths and lengths. Bonding is achieved by the addition of synthetic resin adhesives, which are cured under heat and pressure. Paraffin wax is added to assist with water repellency, while other chemicals can be added during manufacturing for more specific protection.
MDF is primarily used for internal use applications, in part due to its poor moisture resistance. It is available in raw form with a fine sanded surface or with decorative overlay such as wood veneer, melamine paper or vinyl.
Note: Other general purpose dry-processed fibreboards are available, being Ultra Low Density, Low Density, High Density (HDF) and High Performance (MR only). These tend to be specialty products, so further information about their usage should be confirmed directly with the manufacturer.
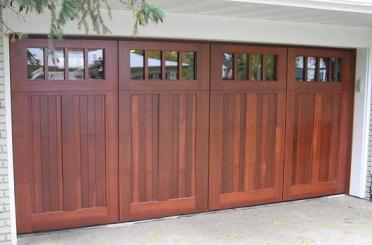
Doors
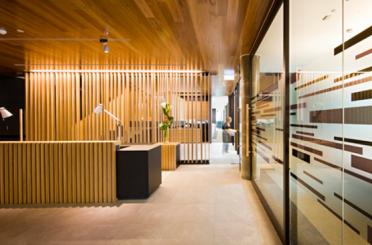
Panelling, Interior
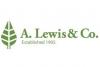
A. Lewis & Co. PTY LTD
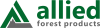
Allied Forest Products
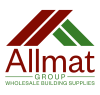
Allmat Timber

Australian Panels
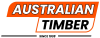
Australian Timber
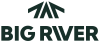
Big River Group
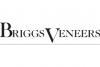
Briggs Veneers Pty Ltd
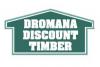
Dromana Discount Timber
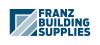
Franz Building Supplies
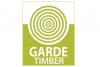
Garde Timber Pty Ltd
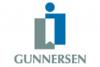
Gunnersen Pty Ltd
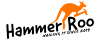
Hammer Roo
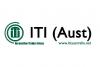
ITI (Australia)
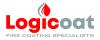
Logicoat
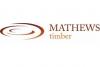
Mathews Timber Pty Ltd
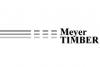
Meyer Timber Pty. Ltd.
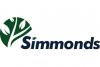
Simmonds
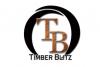
Timber Blitz Pty Ltd
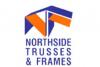
Timbertruss Northside
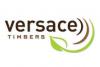