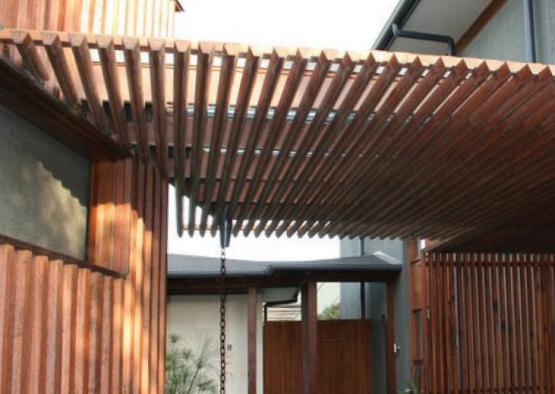
Sawn timber is timber that is cut from logs into different shapes and sizes. Sawn timber is generally cut into varying rectangular widths and lengths, but may also be wedge shaped. Common sawn timber products include solid timber beams and more rectangular timber sections.
Log preparation
The first step in the conversion of logs to wood is the preparation of the log. The branches and bark are removed from the tree trunks prior to any processing. Removing the bark leaves all the heartwood, and most of the sapwood. This process now takes place in a matter of seconds on the forest floor with specialised machinery.
Where the logs are to be used as poles or piles, some specifications may call for removal of the sapwood. This can shape the log so that it is perfectly round, has sixteen or more faces, or is true to the original shape of the tree.
Processing
Logs classified as ‘saw logs' are sent to a saw mill to be processed. Logs are stockpiled under water sprays to prevent them from splitting as they rapidly dry out.
The logs are then sawn into rectangular shapes in the ‘green mill'. Here the logs are fully saturated and the saws leave a rough surface on the wood, as some of the fibres are torn out rather than cut.
If timber is to be seasoned, or dried, then this will takes place next with the removal of much of the moisture from inside the timber. Seasoned products are then machined to give smooth or shaped surfaces.
Log breakdown
Logs present handling difficulties due to their cylindrical shape, so the first steps in a normal saw mill operation involve cutting the logs to provide flat surfaces. There are many different cutting patterns used to produce timber - the following are two examples:
- Splits - the first saw cut is through the centre of the log to give two splits, each of which has a flat face for registering in further cutting operations. A characteristic of splits is that the pith is always on or close to one edge of each of the splits. Some timber cut using this pattern will have the pith on or near an edge.
- Cants - the first saw cuts go either side of the corewood in the very centre of the log. The pieces that are left on the outside are called wings, and the almost-rectangular piece from the centre is called a centre cant. A characteristic of the centre cant is that the pith is always in the centre of a big piece of wood. This is known as ‘boxed heart'. Corewood can cause problems where it is close to one corner or edge. This cutting pattern allows the corewood to be locked into the centre of a reasonable sized section.
Green sawn
Once some flat surfaces have been established by the breakdown saw, the other saws in the green mill can cut the various pieces into marketable timber. Each mill establishes its own cutting patterns for different sized logs, in an attempt to maximise the number of pieces cut in the most popular sizes.
Sawing patterns
Each cutting pattern produces timber with a distinct appearance and character. Each type has its advantages and disadvantages.
Quarter sawn timber
Also called quarter cutting, with quarter sawn timber the growth rings are parallel to the short face. The long face of every board is close to a radial face. A large number of growth rings can be seen on this face. Quarter sawing timber is best for hardwood species that are prone to collapse during drying.
Quarter swan timber has the following advantages:
- Best grain shows on face
- Good wearing surface for floors, furniture
- Radial face preferred for coatings
- Lower width shrinkage on drying
- Less cupping and warp than other cuts
- Can be successfully reconditioned.
The disadvantages of quarter sawn timber include:
- Slower seasoning
- Nailing on face more prone to splitting.
Back sawn timber
Also known as back cutting and tangential cutting, back sawing is the most common sawing method used in Australia. Back sawing helps to obtain high-grade timber from logs.
Most structural timber and many appearance products are backsawn. With backsawn timber, the long face of each board is close to a tangential face, and the short face is close to a radial face.
Growth rings are parallel to the long edge and the wide face does not intersect many growth rings. The growth rings on the wide face appear to be very wide apart, and some interesting patterns can be seen.
This cut offers more flexibility in that quite large boards can be backsawn from the wings of logs. Here the maximum depth can be just less than the diameter of the log.
Back sawn timber has the following advantages:
- Seasons more rapidly
- Good figure on face
- Less prone to splitting when nailing
- Wide sections possible
- Few knots on edge.
The disadvantages of back sawn timber include:
- Shrink more across width when drying
- More likely to warp and cup
- Collapsed timber more difficult to recondition.
Radial sawn timber
This cut is not very common, and if required would need special negotiation with the mill. However, radial sawing has an efficiency that the other cuts cannot achieve, and makes optimal use of a log.
Because of the cutting pattern, each piece of radially sawn timber is a wedge shape. It has sapwood on the wider edge and pith or corewood at the point.
As real logs are not perfectly round and not perfectly straight, each radially sawn board reflects the longitudinal shape of the log.
These details can make for interesting architectural use of the timber. Apart from flooring, radial sawn timber is used mainly for external applications such as cladding, decking, poles, wedges and timber screens.
Radial sawn timber has the following advantages:
- Dimensional stability
- Less prone to warping, cupping
- Less wastage in milling.
The disadvantages of radial sawn timber include:
- Wedge shaped cross section
- More difficult to detail
- More difficult to stack.
Sawn timber will either be available as unseasoned or seasoned:
- Unseasoned timber - is classified according to its moisture content. Any timber with a moisture content > 25% is said to be unseasoned or ‘green'. However, for practical reasons, most timber sold as unseasoned has a moisture content > 15% rather than the more strict definition of unseasoned timber (> 25%).
- Seasoned timber -producing seasoned timber is the process of drying timber to remove the bound moisture contained in walls of the wood cells. Seasoning can be achieved in a number of ways, but the aim is to remove water at a uniform rate through the piece to prevent damage to the wood during drying (seasoning degrade). Seasoned timber has a moisture content between 10 and 15%. Timber in this condition will be in equilibrium with internal environments in many parts Australia.
Seasoned timber has a reduced weight, improved strength and the cross sectional dimensions remain almost constant. It is more stable than unseasoned timber and is much less prone to warping and splitting. It also provides improved gluing and nail-holding properties and increased joint strength.
In higher grades of timber, particularly hardwoods, the process of seasoning can enhance the basic characteristic properties of timber, increasing stiffness, bending strength and compression strength. Seasoned timber should be chosen for indoor use where it is particularly important not to have shrinkage associated with drying out in service.
Kiln drying timber
The most common commercial processes for seasoning of timber is kiln-drying. Kiln seasoning accelerates the process of seasoning by using external energy to drive the moisture out.
The timber is stacked in much the same way as it is for air drying, and is placed inside a chamber in which the conditions can be varied to give best seasoning results. Air is circulated around the charge (stacked timber) and the temperature and humidity can be varied to give optimum drying. Each species has different cell characteristics and therefore requires different drying schedules. Typically the timber may be in the kiln for a period of between two days to one week.
Generally, it is not feasible to kiln-dry structural timber in thicknesses greater than 45 mm, although there are limited amounts of 70 mm thick kiln-dried softwood members in the market place. All untreated structural pine and some commercial hardwoods are seasoned, mostly using kilns that are often heated by sawmill by-products or gas.
Kiln-seasoning of softwoods such as pine can be done fairly quickly, however seasoning of hardwoods tends to be a much longer process, due to the different cell structure of hardwoods.
Air drying
The traditional method of seasoning timber was to stack it in air and let the heat of the atmosphere and the natural air movement around the stacked timber remove the moisture. The process has undergone a number of refinements over the years that have made it more efficient and reduced the quantity of wood that was damaged by drying too quickly near the ends.
The basic principle is to stack the timber so that plenty of air can circulate around each piece. The timber is stacked with wide spaces between each piece horizontally, and with strips of wood between each layer ensuring that there is a vertical separation too. Air can then circulate around and through the stack, to slowly remove moisture. In some cases, weights can be placed on top of the stacks to prevent warping of the timber as it dries.
Moisture loss from the side of the wood is at about the correct rate so as not to cause collapse of the cells, but near the ends of the wood, the moisture loss can prove to be too fast. Often the ends are wrapped or painted to slow the moisture loss from the end grain.
While little additional energy needs to be supplied for this type of seasoning, the stacks of timber require a lot of land, represent a potential fire hazard, and the product is not able to be sold for a considerable time.
Air-drying of timber is really a more controlled facilitation of what happens to unseasoned sawn timber, once it is placed into its ‘work' environment. The amount of drying that can occur is decided by the relative humidity of the drying environment and will often vary within individual boards as well as within the stack itself. The time taken for air-drying is a function of the thickness of the timber.
Air-drying is a slow process, particularly for hardwoods, typically taking 6 to 9 months to reach a moisture content in the range 20% to 25%.
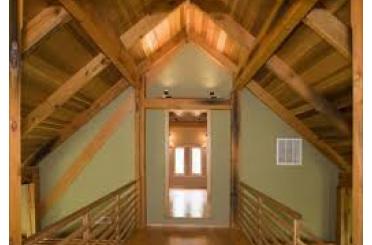
Architectural Roof Trusses
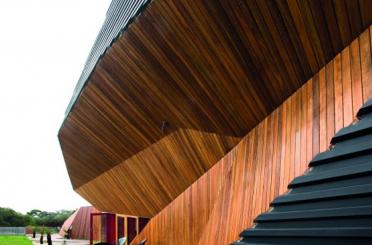
Cladding, External

Decking
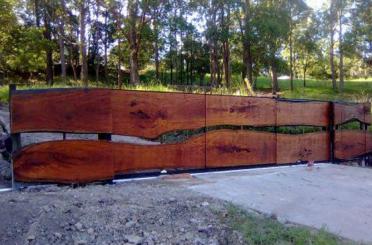
Fencing
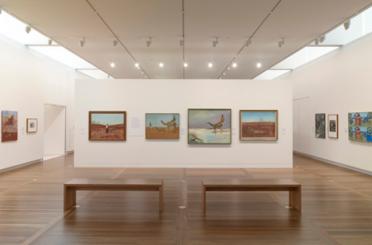
Flooring
Framing
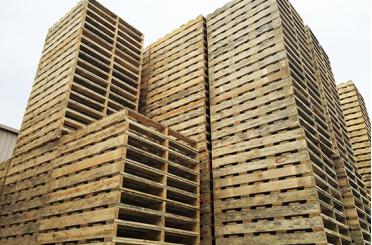
Packaging
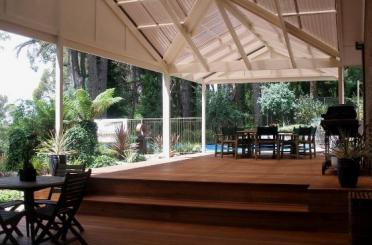
Pergolas
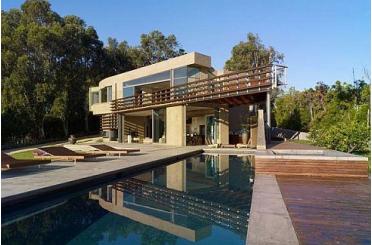
Rails and Balustrades, Exterior
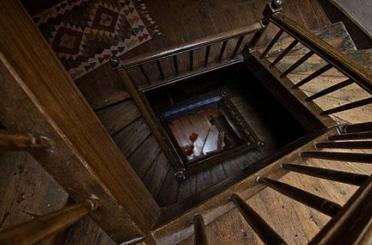
Rails and Balustrades, Interior
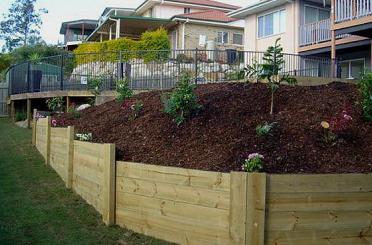
Retaining Walls (Landscaping)
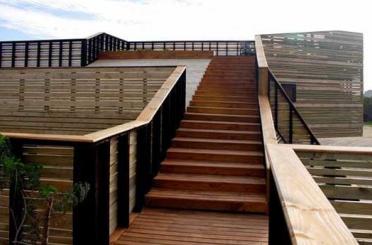
Stairs, Exterior
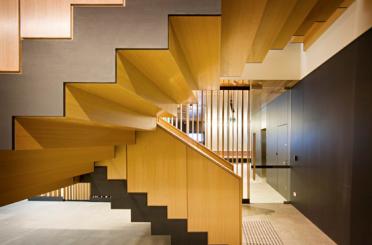
Stairs, Interior
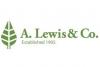
A. Lewis & Co. PTY LTD
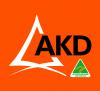
AKD Softwoods
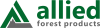
Allied Forest Products
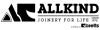
ALLKIND Joinery
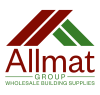
Allmat Timber
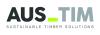
Austim Pty Ltd
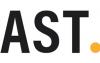
Australian Solar Timbers
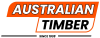
Australian Timber
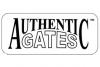
Authentic Gates Pty Ltd
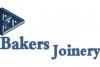
Bakers Joinery
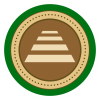
BAYWOOD
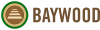
Baywood Products Pty Ltd
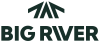
Big River Group
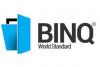
Binq Windows & Doors
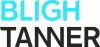
Bligh Tanner

Branch 95
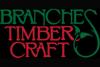
Branches Timbercraft
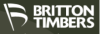
Britton Timbers
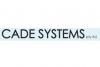
CADE Systems Pty. Ltd.
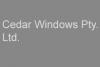
Cedar Windows Pty. Ltd.
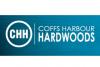
Coffs Harbour Hardwoods
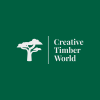
Creative Timber World
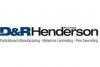
D&R Henderson Pty Ltd

Decking Perth
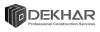
Dekhar Outdoors
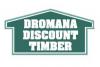
Dromana Discount Timber
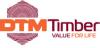
DTM Timber
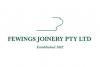
Fewings Joinery Pty Ltd
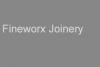
Fineworx Joinery
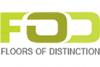
Floors of Distinction
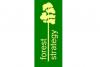
Forest Strategy Pty Ltd
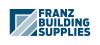
Franz Building Supplies

Future Windows
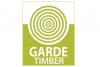
Garde Timber Pty Ltd
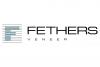
George Fethers & Co.
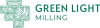
Green Light Milling
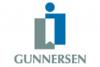
Gunnersen Pty Ltd
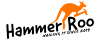
Hammer Roo
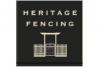
Heritage Fencing
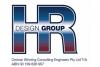
HR Design Group Pty Ltd
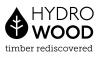
HYDROWOOD
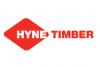
Hyne Timber
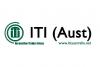
ITI (Australia)
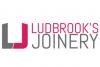
Ludbrook’s Joinery
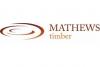
Mathews Timber Pty Ltd
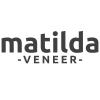
Matilda Veneer
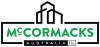
McCormacks Australia
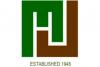
McKay Joinery
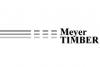
Meyer Timber Pty. Ltd.
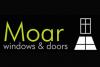
Moar Windows & Doors
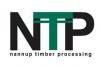
Nannup Timber Processing
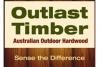
Outlast Timber Supplies
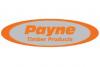
Payne Timber Products
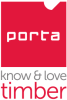
Porta
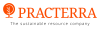
Practerra
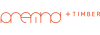
Premind Timber
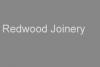
Redwood Joinery
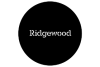
Ridgewood Timber Pty Ltd
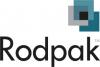
Rodpak Pty. Ltd
Ryan & McNulty Pty Ltd

Sashman Pty Ltd
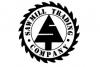
Sawmill Trading Company
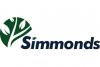
Simmonds
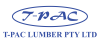
T-Pac Lumber Pty Ltd
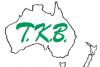
Tasman K.B Pty Ltd
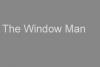
The Window Man
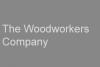
The Woodworkers Company
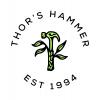
Thor’s Hammer
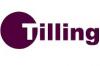
Tilling Timber
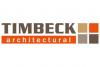
Timbeck Architectural
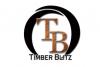
Timber Blitz Pty Ltd
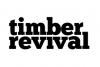
Timber Revival
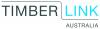
Timberlink Australia
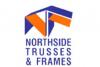
Timbertruss Northside
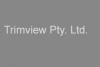
Trimview Pty. Ltd.
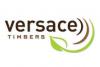
Versace Timbers
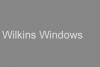
Wilkins Windows
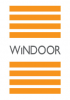