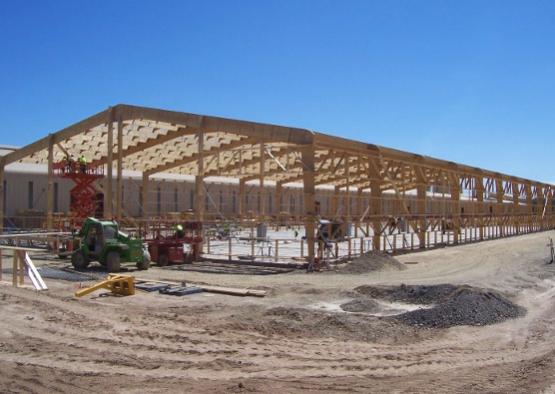
Overview
Engineered timbers perform better and are easier to work with than steel in large commercial and industrial structures. In some applications, LVL may be cheaper; in most, it is definitely no more costly than steel.
When Alpine MDF Industries needed a new warehouse for its MDF moulding plant and pre-prime paint line, it looked to its sister company in New Zealand for inspiration. Nelson Pine Industries had successfully completed two much larger warehouses in New Zealand, where LVL is becoming the preferred material for certain types of commercial and industrial frame construction.
Don't be put off by international and Australian code differences for timber structures. Structural engineer Peter Dixon has shown that, with some extra attention at the design stage, you can readily verify structural adequacy for building loadings that meet Australian building codes.
That little bit of extra effort at the design stage is more than rewarded during construction. "With a timber structure, the builder can do all the work in-house and onsite," said David van Zanten of Southern Cross Developers. "The project is easier to manage and the turnaround time is shorter."
Structure
From the outside, Alpine MDF Industries Warehouse/Plant Facility looks no different from the other buildings in the complex. However, unlike the other warehouse-type structures, its cladding of Colorbond steel is secured to a timber frame 80 metres long by 30 metres wide.
LVL is a strong, stable structural material that can be engineered into long lengths and large sizes, reducing the number of joints needed. Generally however, sizes need to be larger than a comparable steel member. Andy van Houtte selected LVL 11 H2 for this project to keep the number of joints to a minimum. "LVL has the added advantage of excellent fastening properties because the veneers overlap each other," he said.
The timber members were shaped onsite and nailed together according the engineer's precise specifications. The nail pattern is critical in timber structures, and Contract Administrator David van Zanten created more detailed shop drawings for his carpenters to follow.
LVL is flexible, so the sections needed to be built on the ground then hoisted into place. This was achieved through an innovative double rafter system that lapped onto the outside of the central column and used a pivoted portal leg. This allowed for the roof bays to be constructed on the concrete pad and lifted into position using a crane. It also made for simpler joint details with less nailing, and substantially reduced the risk of working at height.
The completed structure has several advantages, including being bird-proof - a very important criterion for some buildings. "With LVL, the purlins are flush with the top of the rafters, allowing roof cladding to be fastened along the length of the structure," said Structural Engineer Peter Dixon. "Further, roof end braces are compression diagonals in the end bay of the roof and second bay of the wall, eliminating crossed tension braces where birds may nest."
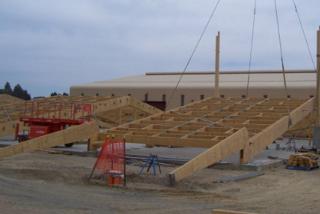
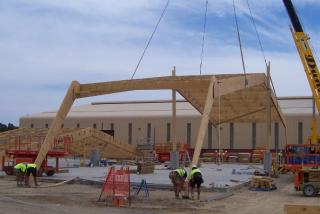
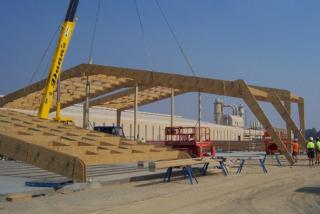
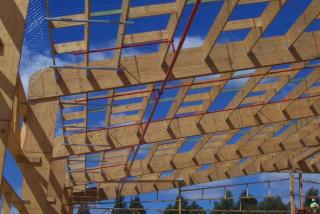
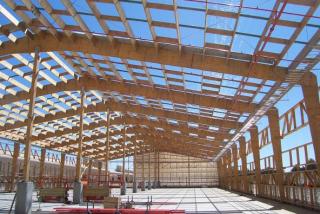
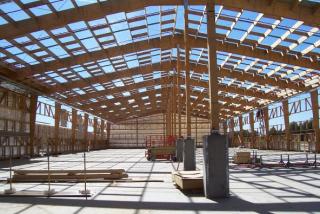
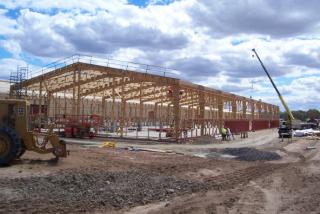
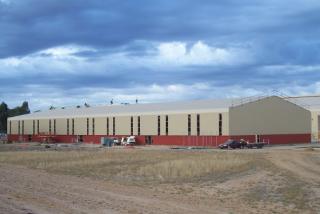
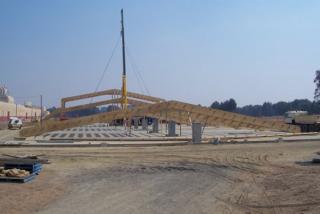