Bondi Beach
Sydney NSW 2026
Australia
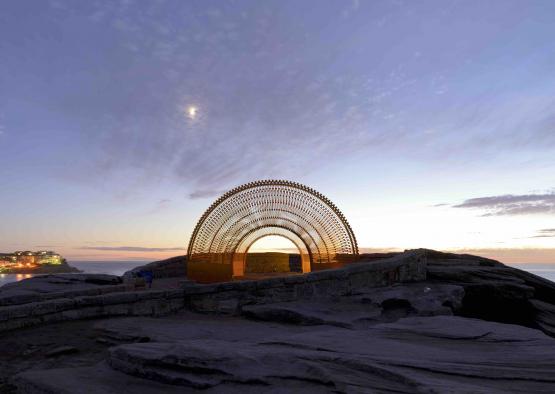
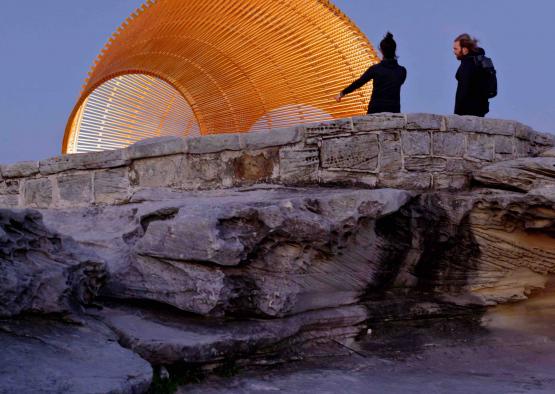
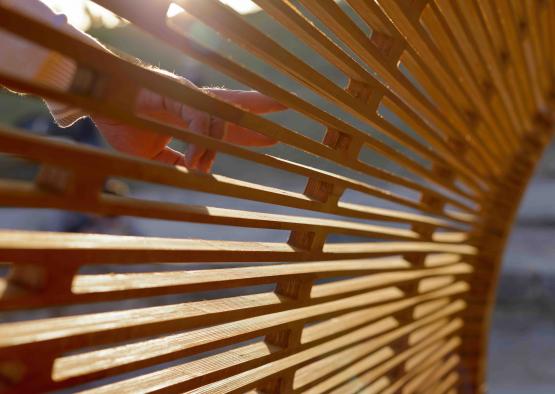
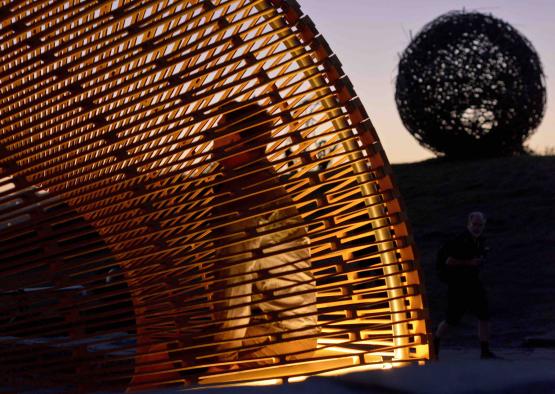
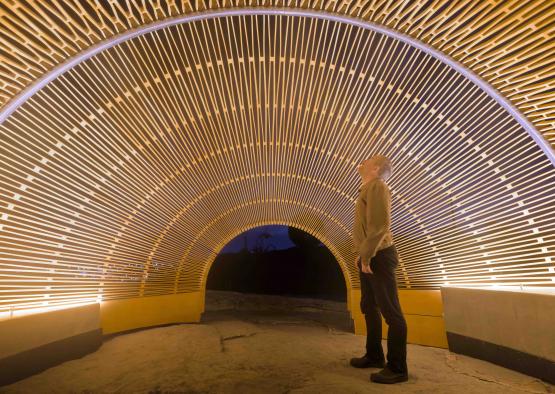
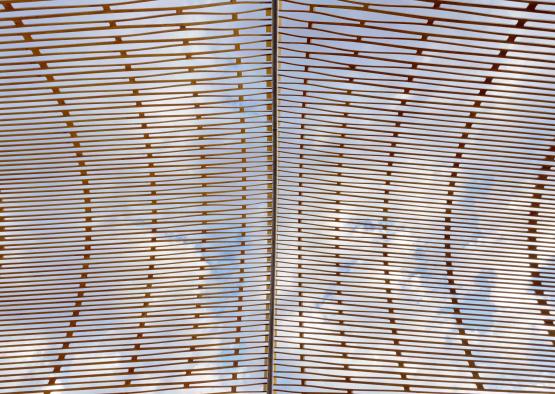
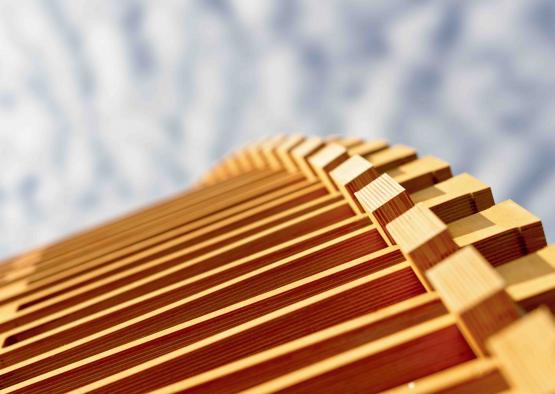
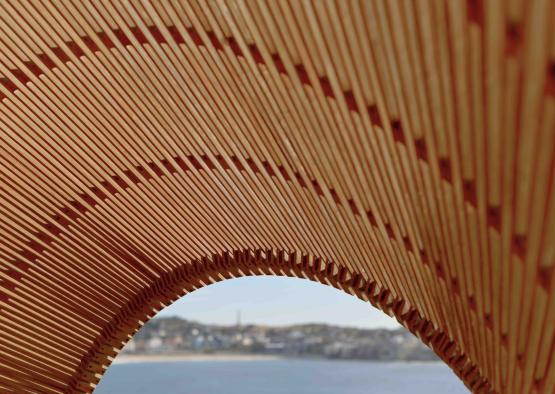
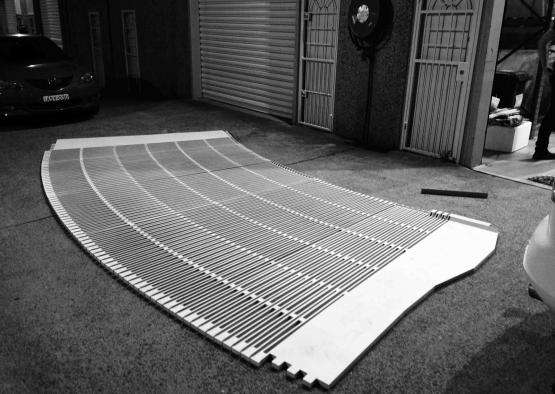
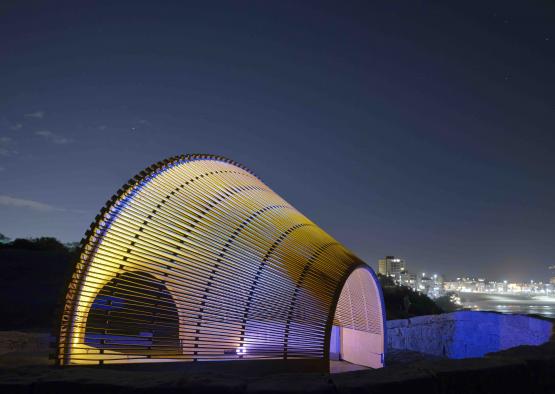
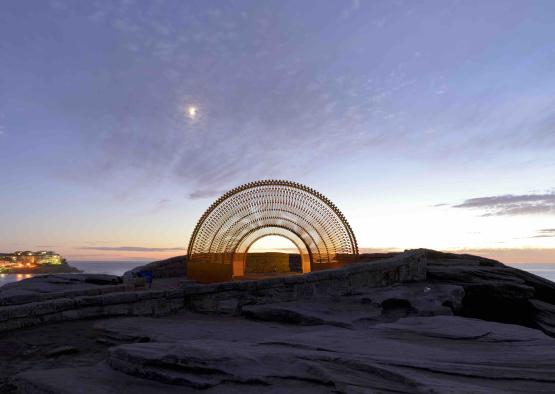
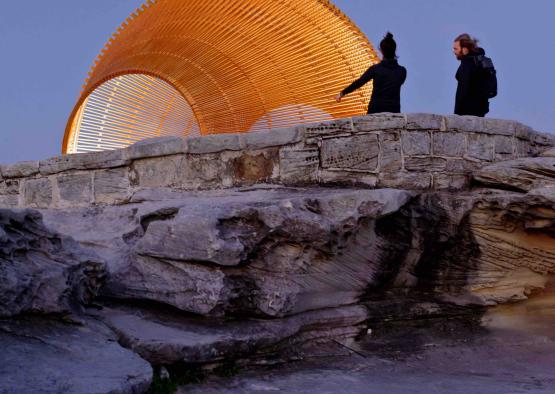
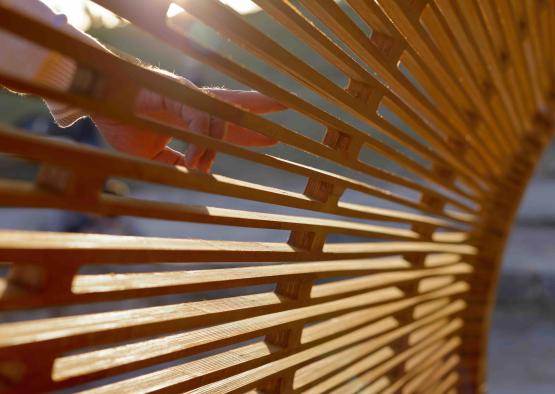
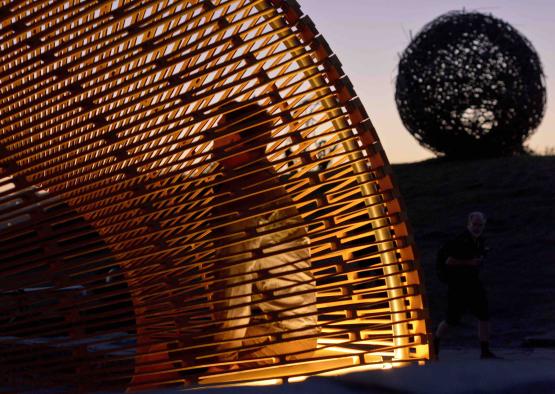
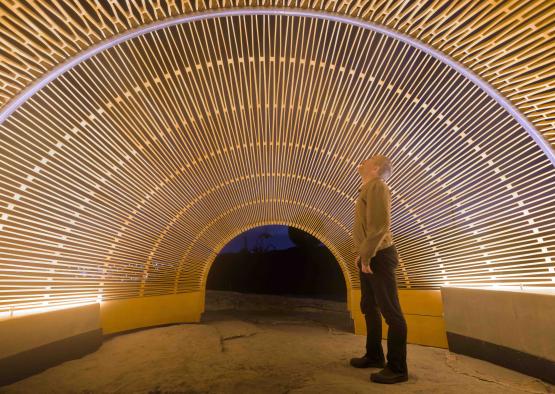
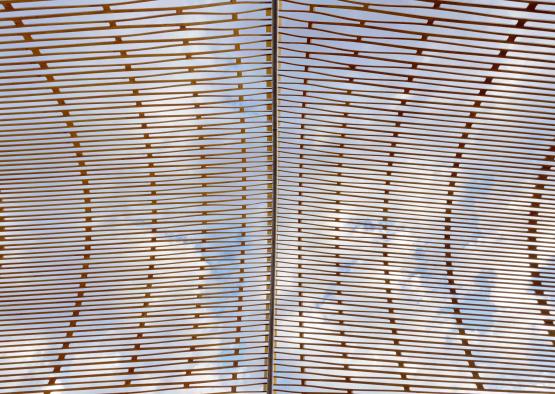
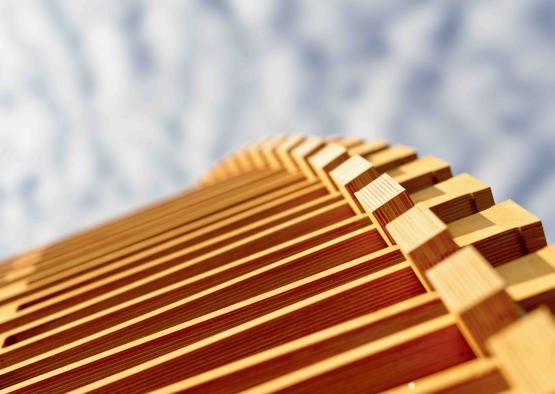
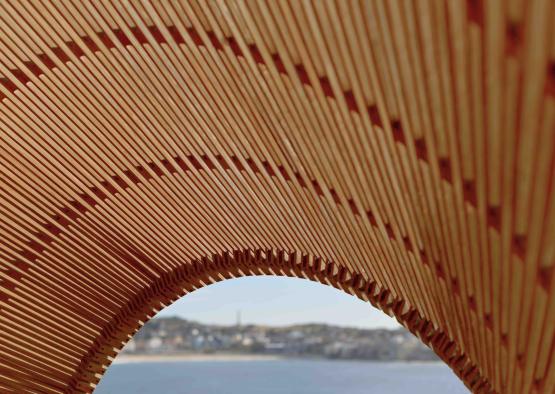
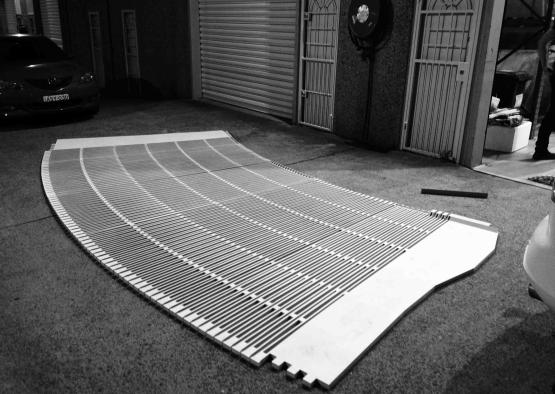
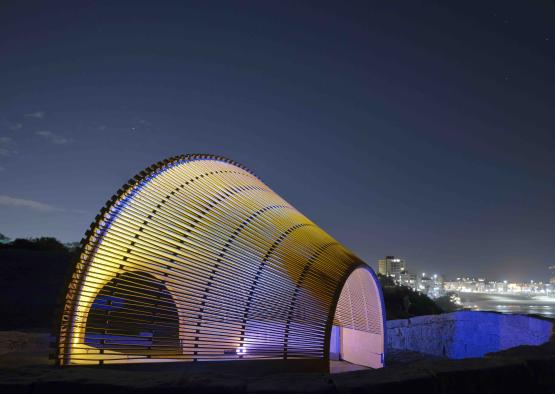
Overview
Produced for exhibition at Sculpture by the Sea, Bondi, this piece is a freestanding pavilion constructed from birch plywoood. Its iconic and distinctive form is a direct product of the versatile material properties of plywood and an unconventional approach towards design and fabrication. Fundamentally, the piece aims to exploit the lithe properties and engineered strength of birch ply. This was coupled with precision digital fabrication to create a timber structure which acts as both robust exoskeleton and supple skin. Being otherwise seperate but parallel undertakings, design and fabrication were fused into one process to produce this piece. In this, the design moved fluidly between physical prototypes, sketches and documented designs. Detailing was also driven by this process, minimising mechanical fixings and allowing the plywood to act as a free standing shell. It is an exemplary project for it's pursuit and celebration of new frontiers in timber material performance.
-33.8914755, 151.2766845
Structure
The pavilion is comprised of two continuous, flexible sheets of plywood, each measuring 2400 x 7800mm. The sheets have been cut to a precise pattern that carefully exploits the flexibility of the material while maintaining its structural integrity. This allows the plywood to perform in a lithe, textile- like manner, fanning out along one edge and bunching along the other. Layered into this was consideration for the fabrication parameters and efficient workflow. Each slot also tapers in plan view to ensure the plywood is of a consistent flexibility from the outer edge to the spine. This was introduced in response to challenges ensuring the plywood shell fanned out correctly without excessive bunching or lack of flexibility.
Given the innate movement of the plywood, direct screw fixings to the steel would tear through the birch under high wind loads. Therefore, mechanical fixings were not used and instead the rods have been concealed within the plywood, allowing free movement around the steel. The central spine was clamped to the CHS by tensioning a cable over the top valley sandwiching the plywood spine in place. Each finger of the plywood along the spine was dovetailed so that the two shells interlocked when joined.
Taubmans Timber Pro Natural Oil, a water based exterior grade oil, was used to protect the plywood. Given the extent of end grain exposed coating these areas was critical to ensuring the longevity of the plywood. Water based oils were used in this instance to avoid crazing.
The innovative use of birch plywood in this project can be realised when the pavilion is understood as a two halves of a shell. Each half is a flexible, continuous sheet of plywood measuring 2400 x 7800mm. The sheets have been cut to a precise pattern that carefully exploits the flexibility of birch plywood while maintaining its structural integrity. This allows the plywood to perform in a lithe, textile-like manner, fanning out along one edge and bunching along the other. Birch plywood was selected for this structure as a hardwood with a significant capacity for tensile strength. It's innate properties allow it to fan out in two directions which is critical to achieving conic forms Birch plywood is also a marine grade plywood ideal for CNC milling due to it's density and textured grain. This is celebrated in the design of the pavilion exposing and embracing the end grain pattern unique to plywood products. Mechanical fixings have been minimised, instead using the plywood to encapsulate steel and 'zipper' the shell together along a central spine. While on exhibition viewers engaged with the piece, running their hands along the timber and catching the smell of fresh cut birch.
Products used: 100% Wisa BB/BB Birch Exterior Plywood - 30mm gauge, 21 plies of 1.4 mm thick birch veneers.