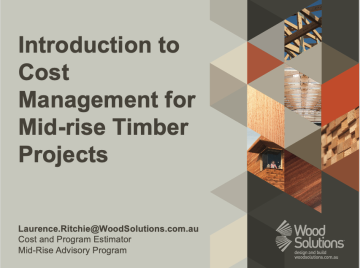
The presenter of this webinar is Laurence Ritchie, a cost expert and member of the WoodSolutions Mid-rise Advisory Team. All are welcome, but this webinar is most relevant to quantity surveyors, builders, developers, investors, and financial institutions.
Engineered timber construction systems are rapidly growing in popularity. With specifiers and developers selecting timber solutions for their financial and environmental benefits and leading builders driving for wood products to improve on site efficiencies, safety and quality, it has never been more important for the cost consulting industry to understand the products available and their cost implications.
This webinar provides an introduction to the products and systems typically used in the delivery of major timber structures. It will present the recently launched WoodSolutions Cost Engineering Guide (completed in partnership with RLB), and will briefly touch on topics including fire protection, durability, acoustics, the supply chain, and project financing.
WoodSolutions Webinars
Good morning, everybody, and welcome to this first webinar of the WoodSolutions webinar series. Each week on Tuesday at 11:00 AM AEST, you can expect a webinar from us on a wide range of topics on timber construction. In today's webinar, we're going to be covering an introduction to cost management for mid-rise timber projects. This will be presented by Laurence Ritchie, who is the cost and program manager with the Mid-rise Advisory Partnership.
My name is Adam Jones. I'm a structural engineer with the Mid-rise Advisory partnership as well, and I am the host of the WoodSolutions Timber Talks podcast. If you haven't heard about WoodSolutions before, I'll just talk a little but about what we do. We're funded by Forest and Wood Products Australia. We are a not for profit, and basically we exist to help everyone listening on this webinar right now to go out there and design and build in timber. The way we do that is we've got a wide range of resources. Most famously probably are the WoodSolutions Technical Design Guides. Right now we've got 51 of them, and topics range from structural engineering to architecture to cost management to detailing to durability. So, any questions you have, will probably be able to be answered within these guides.
We've also got WoodSolutions Campus, so right now is probably a good time to go out and up skill if you find a bit of time up your sleeve. So, all the courses on WoodSolutions Campus are free. At the bottom here, the team I'm part of, and same with Laurence, is the mid-rise advisory partnership. We've got all the partners you can see on the bottom of the screen here, and we exist to give free technical support to real mid-rise projects. So, say if you've got a project that is currently documenting concrete and you're interested to see what the timber solution might look like, we've got a costing engineer, a structural engineer, a fire expert, an architect on the team, so we can go from different angles and comment on the feasibility about your project. So, feel free to get in touch with me if you want us to look at some of your projects.
This is some of the functions that you can see using Zoom webinar. On the bottom left hand side of the screen, you've got the chat function, and the bottom right hand side of the screen here you've got the Q&A. With the chat function, I recommend everybody feel free to introduce yourself and ask some of the questions if you like here, and there's a lot of experienced people who are attending this webinar, not just the people who are panellists and presenters, so feel free to have a robust discussion in the chat, or at the end of the session we'll be going through the Q&A with the two presenters, or Laurence Ritchie, who's a presenter, and the panellists, Paolo Lavisci. You've also got the ability to up vote the questions that you think are most relevant and the questions that you like the most.
This is a webinar series, so today is the first one. We're going to have Laurence Ritchie presenting, and Paolo Lavisci as the contributing panellist member. Next week's webinar at Tuesday at 11:00 AM, we're going to have design optimisation using parametric design with Richard Maddock. This is a very interesting topic as well. As you can see here, parametric design and structural optimization can get some really interesting architectural solutions, so this is the set up out in England, and using all the exciting, innovative, cutting edge technologies like Grasshopper and talking about how it speaks to robotics and pre-fabrication techniques and so forth. Make sure you stay tuned and sign up for that, which I'll be sharing with some links after this webinar.
Here's a little teaser for upcoming topics, building in a bush fire prone area, a range of case studies, sustainability topics, more structural engineering topics, and so forth. There has been a few questions already asked from Carol, Robert and Jacinta regarding the CPD forms. This is a formal CPD event, so if you were tuning in for our previous webinars, they were informal CPD. This is different in that it is formal, meaning we get to give you three questions and you have to answer three questions to achieve this formal CPD. And we're going to send you a SurveyMonkey after this with these three questions and also give you the ability to download the form yourself. This is the form that you'll get on the left hand side of the screen, and you can fill out yourself, and this will be your formal CPD certificate. So, I hope I answered that properly Jacinta, Carol and Robert, but if not, please let me know in the chat and I'll go through it again at the end of this webinar.
Okay. Without any further ado, we'll get into the first part of this webinar, which is Laurence Ritchie presenting. Laurence has a master's degree in construction management, experience in T1 construction, and over a decade working in the property sector. Drawing on the holistic understanding, Laurence engages in project evaluation and design optimization services, ultimately requiring estimation of construction programme and costs. With a keen eye for detail and a passion for innovation in construction, Laurence sees the opportunity for timber systems to change the way we build for the better. Right now, I will pass it over to you, Laurence. I'll make you a host and you should be able to take the screen over.
Laurence Ritchie
Looking good. Share screen. Yep. All right. I'll just quickly make you a host again, Adam.
Perfect. Cool, all right. G'day, everyone. Thank you very much for coming along, and thank you, Adam, for the kind introduction. As Adam suggested, my name is Laurence Ritchie. I work as part of the mid-rise advisory programme as a cost and programme estimator. We have an interesting role, which is purely advisory. We don't charge for anything we do. We're funded by the industry and then partially by the government under a voluntary matching scheme, and basically we can support you in any of your projects, whether it is in the realms of costing, which of course we're talking about today, structural engineering, or any of those other areas, as Adam was saying.
Today we're talking about an introduction to cost management for mid-rise timber projects. Now, the important word here is introduction, of course, because this is the first presentation of what is expected to be a series. We're going to touch on a number of different topics relatively lightly, given the time frame that's available, and then we'll delve a little bit further into those in future webinars. We're going to start off with a bit of context about what we're talking about and why it's relevant to the industry today. We're going to look at our cost engineering guide, which as Adam briefly mentioned is a recent technical design guide which was launched last year, touch on a system, which is the system, I should say, which is a really important part of all this, in my opinion, and obviously we'll conclude.
So, as a bit of an introduction, in 2016, in case you're not aware, the National Construction Code changed to allow timber structural systems in buildings up to an active height of 25 metres. That's about eight stories in height, and you can see in the little graphic here, it's really what we classify as mid-rise, that four to eight story space. In 2016, that was classed as two, three and five, so it's typically apartments, hotels and offices, and in 2019, these provisions were expanded to all building classes. So, you can build any of these typical buildings, whether it's a hospital or a school, an aged care home, as a deem to satisfy solution under the National Construction Code.
Since that time, we've seen... sorry, let's try again. Since that time, we've seen a lot of growth in this area. We've seen some amazing mid-rise projects coming through. The first project which actually occurred, a mid-rise timber project which occurred with, I suppose, contemporary construction systems in the one on the left hand side here, Forte, and that was built back in 2012 to '13, and then since then, we moved onto a few others, and more recently, a couple of the other buildings that are towards the right hand side here, I think. You might be most interested if you are based in Victoria, in, say, 55 South Bank, which is that central project down the bottom. Maybe if you're up in New South Wales, there's quite a few projects in New South Wales, but Aveo Aged Care, which is up in the top right hand side, that's a nine story, maybe it's a 10 story aged care home built out of timber systems.
We've also seen a lot of projects proceed in the office space, and these are just a few which we've seen over the years and we continue to see under construction at the moment. We can talk about these in a bit more depth at a later date or if you want to contact us directly, of course. We can always talk about them then. The uniting factor in all these projects, of course, is the main structural product used is timber. These are typically the main timber products which we see used in the completion of these buildings. There are other products, I really need to specify, around the world, which are utilised. I know in North America, there's nail laminated timber and dowel laminated timber, there's quite a few more in Europe. But these are typically what we see used the most in our market in Australia.
We can really group these into two different categories. The one in the darker circle we would classify as light weight systems, and that's really everything which you might see if you go out to a growth suburb. Really, really common for us to build our houses out of light weight systems with stud framing and light weight trust floors or roofs. Then the other option is in those lighter circles, what we'd classify as massive timber. As you can see, those products we typically see in that category. Gluelam or glue laminated timber, cross laminated timber, or CLT, and laminated veneer lumber, or LVL. We'll go into those just in a little bit more depth just so we can see how they relate to the mid-rise space.
So, light weight framing. This may surprise some people, but light weight framing is actually a really good, efficient solution to mid-rise apartments or cellular construction. You can see here this is a beautiful project completed out in Melbourne's west, which as you can see, it's five stories in height, and it's built using stud framing. The really simple thing around stud framing, the amazing thing about stud framing is that studs can come in different grades and of course in different sizes as well. As the loads increase in a project, you can simply just increase the grade of the timber that you're using in the stud, whether that be an MDP 10 up to 12, or then even up to 15, or you can even take it to LVL studs and you can deliver obviously a beautiful high quality outcome like this.
CLT or cross laminated timber, you're likely to have heard of before. It's been a bit of a buzzword, especially on Grand Designs. Basically, this is a product which is made out of layers of timber, or we actually call them lamella of timber, and you can see on my little diagram in the black circle here sort of how it looks. The idea is that each layer runs perpendicular to the one either side of it. They're all glued together and pressed together, and that creates a solid wood panel, which can then be used as a two way slab for a floor, it can be used as a sheer wall, it can be used as a wall for other purposes as well, and it's generally a very effective panelised product. So, you can see here, this is a beautiful project from down in Victoria, Melbourne's south east down in Frankston, which is a student accommodation project for Monash University.
Laminated veneer lumber is another one of these massive timber products. But the interesting thing about LVL is that it can also be cut down to be considered to be a lightweight product like a stud. The way LVL is produced is it's made out of veneers, as you may expect from the name, which are three to four ml thick layers of timber, which are actually peeled, rotary peeled from a tree. What that means is that you can align all of these veneers, so the gain is going in the same direction. You can glue them and press them together, and that creates an incredibly strong structural element, particularly when you're going parallel to the grain, so as an axial load, as we can see with this column just here, which is really a mega column.
With the LVL produced in Australia, we know that the compressive strength parallel to the grain is typically between 47 and 51 MPA, which is quite amazing when you consider that high strength concrete is considered to start at 50 MPA, where essentially we've got this great natural renewable resource of high strength timber. It's a really, really interesting product, and obviously potentially very efficient on your project, given the design. Finally for the massive timber system or massive timber products, we've got glulam, or glue laminated timber. This product kind of draws a little bit from LVL and a little bit from CLT in that it's made out of solid pieces of wood, not veneers, similar to CLT. But like LVL, all the grain goes in the same direction.
What we typically see with glue lam is that it is best used as a column or a beam. You can sometimes use glue lam as a floor panel or as a wall panel if you can make it a wide enough beam or a wide enough element, but of course that's subject to your design and subject to your supplier's abilities. And as you can see, you can create these really beautiful high span open floor plan environments, and, yeah, we've seen that really take off around the country in the form of office developments but then also education as you can see here. This is at RMIT University in Melbourne. Finally, we've talked about timber for everything so far, but it's really important to note that you can build composite structure.
Composite structures have been shown to be really effective where they're needed around the world. I know in the UK there's been a lot of work done with steel framing and CLT floors, and we have seen that in Melbourne, Australia as well, where we've got this great six story vertical extension, which is this bit here, over an existing office building in a really, really busy part of Melbourne's CBD. There's the main tram terminus here, there's a big train station just over here. This is corner of Flinders and Elizabeth, to anyone from Victoria, and there would be tens of thousands of people who walk past this every day, so it was very important in this solution that the project was delivered as quickly as possible, but then also without as much disruption as possible.
Now, all of these systems kind of come together, especially where we're talking about the timber systems. They're all made of timber. They all behave in very similar ways in different temperatures and moisture levels. So, they can work really well as a composite of timber. If you're interested to learn a bit more about that or a bit more about the products specifically, I recommend having a look at our technical design guide 46, which as Adam was saying, is available for free from our website as part of the full suite of which all the guides are available for free. So, on that note, let's jump into the cost engineering guide and look at some costing in a bit more detail.
Firstly, as I was saying, we do have this wide range of guides which cover everything from durability through to fire through to acoustics, and then of course we've got a few on costing as well. So, these are our three guides, which are specific to costing. 26 and 27 were completed a couple of years ago and updated 2018 and then 2019 as well. They basically provided direct cost comparison between a concrete building and a timber building, which delivers the same design, essentially. Really interesting guides to go and have a look at. We didn't do them. I didn't do them personally. I actually wasn't with WoodSolutions when they were done, but they were actually completed by a quantity surveyor up in Sydney who also works in Melbourne called MBM. Of course, we gave them the designs, and they went off and did their thing. So, we're quite comfortable that they are quite, I suppose, credible.
Technical design guide 51 is the one, of course, that we're looking at today. We have completed this over the last year, year and a half or so. We launched it towards the end of last year, and of course they are all available for free to download. Tech design guide 51 covers these main areas, and we're just going to touch on each of these quickly as part of this presentation, and then as I said, we'll go into a bit more depth on some of these topics in the next couple of months as a standalone webinar or on its own. So, if you do have really detailed questions, of course we're happy to look at them today. I suspect there might not be time, but if there is, that's great. But if we don't have time today, of course we're happy to answer them later, or as one of these more direct detailed seminars on those topics.
The guide finished with an appendix, which is actually on the execution of timber structures, or I should say the installation of timber structures. This can be really helpful for a quantity surveyor or anyone who has to go out and do an inspection on a mid-rise timber construction site, or anyone involved in the actual construction of the building, because it covers details like how you control for moisture, the tolerances. You should be looking for the types of connection and the right way for them to be completed, and it's generally a useful resource for you to consider during the inspections or during your construction. The guide itself is actually informed by this database of 26 mid-rise or tall timber projects from around the world. A large chunk of these are from the Australian market. I'd say the majority are actually from the Australian market. But then we have also gone out and we worked with friends overseas to source information about projects in really comparable markets to Australia.
The UK, Canada, there's a couple of them, statesides from the US on here as well. Yeah. Basically, these numbers have been used to sort of help the advice that we're giving in this guide and to help complement our previous experiences as well. It's well worth going back and having a look at this in the guide itself. So, moving on through the guide, the next section that we should look at is actually estimating. Now, this is really a very important section obviously for anyone involved in a timber project, because it's where a lot of the questions come from, especially the question of is it cheaper, is it more expensive, and there's a lot that we have to consider in this section, as you can see.
We've got really eight major topics here, which we could probably spend an hour on each on its own, so we're going to touch on them very, very quickly here, and we can come back with questions a bit later on. You'll notice I've made a different colour for the prelims, labour and program on the right-hand side. That's because they're kind of grouped. They are individual and they're in their own right. They do all affect each other, for sure. We'll also touch on those together. Then of course there's the hot topics, if you'll excuse the pun, of acoustics and fire. Of course, we field these questions a lot. But we do find there's a lot of questions out in the industry, so we're more than happy to provide a bit more information on that, but we're going to come back to this, because that is a lot of information, and I want to cover off on the rest of the guide quickly before we come back to the estimate.
The next section in the guide is looking at procurement. Now, you may hopefully understand most of these forms of procurement typically, whether we're looking at a traditional lump sum contract, designer construct, or ECI – early contractor involvement. We typically find that timber construction can work under any of these procurement models. It's not a problem, no matter which one you choose, but we do find that most of the projects are particularly successful when you have an early contractor involvement, and really interestingly, taking it a step further and going early supplier involvement. So, if you can work out maybe who your preferred supplier is or maybe if there's a subcontractor who can supply and install, start working with them nice and early and you'll make your experience much easier throughout the delivery process.
The guide covers the supply chain. In Australia, as you may well know, we have a robust local supply chain. It's particularly mature in the lightweight space, but also in the mass timber. It's been really quickly growing in the last couple of years, and it is now supplying really major projects. But as with everything in Australia, we also have quite a large international supplier supply chain, where suppliers, particularly from Europe, perhaps the US one day, but particularly from Europe at this stage, and New Zealand, I should say, have supplied projects in the market. So, it's important to understand the difference between local and international procurement, how it can affect your project from a cost point of view, from a risk point of view, and obviously from the point of view of the overall project success as well. It's well worth having a look in the guide and we can obviously have another session on this as well.
Risk management. This is an incredibly big topic. I've thrown this risk assessment method essentially up on the slide as almost a placeholder while we talk about the actual risk management forms and how the importance of it in timber construction. Obviously, there's a broad number of different risks that you can be looking at. You could be looking at logistical, you could be looking at quality, whether that's on site or in fabrication. You could be looking at financial. There's just so much you can cover in this. We typically find that if we're looking at quality, that the timber construction methods are generally very, very good, because from a fabrication point of view, everything is fabricated in a factory to millimetre tolerance to the designs of the architect or the shop drawer. So, as long as your designs are right, then they will essentially be cut correctly and then they obviously should be pretty easy to install.
On site from a quality point of view, there's obviously a lot to work on from a moisture management point of view, depending on your climate, depending on the specific site conditions, where you are. You may be needing to treat or protect or look after your timber structure in a different way. This is something that's really important for cost estimators to consider, and for the whole project team, I suppose, to look at. Yeah, it's well worth having a look in the guide for a bit more detail there. Design optimization, this is something which we engage in on a day to day basis at WoodSolutions, where we will find projects which are designed in timber or someone who wants to design a project in timber, but of course there is always a more optimised way that it could be delivered, which of course has an impact on the cost and the programme awn.
What we typically see is that the most optimised timber solution is a solution where you use the product where it performs best. For example, we just have an example here of, say, a seven story and an eight story building. In our little diagram on the left hand side, you can see those top three floors. We could say that that is built out of stud framing. The supply chain can supply that very easily, the products can handle those loads very, very easily, and it's just not a problem. It's essentially building a three story house, which we all know we can do with a stud frame. The next two floors down, we're still building the stud frame, but here we're using slightly more robust materials. So, rather than just using an MGP 10 pine stud, we're actually starting to look at LVL, or laminated veneer lumber studs, which you can get in standard sizes, 90 by 45 or bigger or smaller or as you need. We may be looking at doubling up these studs to increase the capacity of that structural member.
As we get down to the lower couple of floors where obviously you have all of the loads of the building above you bearing down on those lower floors, we need to start looking at mass timber products, which can actually handle that capacity. Here we've got a couple of mass LVL panels. We could be looking at CLT, it could be a post and beam design in glulam, and this is really the most optimised format which we see. Having said that, if it's your first project, you can of course look at utilising one structural product the whole way up the building, but it may be a little bit less cost competitive than this really optimised version. We have quite a large life cycle costing section, which I think is a really interesting area. I won't go really in depth here because of course there's a lot of detail, but I will touch on really two topics which are quite interesting.
One is carbon credits. Obviously, we don't have any legislative carbon credits at this stage, but I think we can all agree it's just a matter of time before they do come through. Of course, when we're building this timber, we're using a product which is actually built out to CO2, essentially. It absorbs CO2 as part of its growth and locks it up in the actual wood in that product for the lifetime of that product. So, if you're building a building out of a sequestered carbon, essentially, product, you're locking up that carbon for the lifecycle of the project, and there are obviously real potentials for the carbon credits moving forward. The other one is biophilic design, which you may have heard of. If you haven't, it essentially refers to the impact of being exposed to natural materials and the natural environment on the human body. I'm sitting, or standing in my office, I should say, I've got a nice wood desk, I'm looking out at the trees, I wish this was a timber structure I'm in, but it's not.
By having these around me, I'm feeling calmer, my heart rate is slower, my blood pressure's a little bit lower. It's just this natural sort of intrinsic thing which we have as part of the human body. I think you can all agree, if you're reading a book, you'd rather be reading a book out in the park, in the sun, than being stuck in the back from of a library which is badly lit and you can only see grey things. So, it's a really interesting area, and it's a big, big potential opportunity for timber construction. The last section of the technical design guide is a couple of case studies. This is a really interesting case study which we completed with Rider Levett Bucknall, which you may know. They're a big international quantity surveyor cost management firm. We worked with their Melbourne office to deliver this comparison.
Here we took the design of a concrete building, which was in late design sort of stage, and we redesigned it in timber. Then RLB went off, they spoke with the industry, and they worked out essentially their estimate of the project cost. As you can see here, we saw the timber option come in at about three percent cheaper. This is over an eight story building. There is, of course, there is an opportunity to find more savings in there, we believe, and I think RLB would agree. But I think the really important message here is that we can be building these buildings safer, we can be building them faster, and we can be building them the same price or cheaper, which I think is a really important part of this.
So, for a bit more detail of that, I really recommend going and having a look at the guide. Of course, we're happy to do a similar sort of thing to this on one of your projects, if you're interested. Let's go back to estimating. This is, as I said, a big topic. A lot of really important areas. This is the topic which really can impact the overall cost of your project. We spoke a little bit about the products at the start. You understand there's light weight framing, there's massive timbers, think CLT, LVL and glulam. Let's have a bit of a look at the acoustics. So, when we're talking about acoustic insulation, there's really two main measures that we look at. One is the airborne sound insulation, the other one is called impact sound insulation. They're referred to as RW plus CTR, that's airborne, and LNW, that's impact.
We typically treat the airborne insulation through the addition of mass. So, if we have a concrete slab, obviously that's a lot of mass. It's a very heavy element. That actually deals with our airborne acoustics quite effectively. If we're looking at the impact rating, we typically have to add some form of resilience to the system. That could be in the form of an underlay, it could be in your flooring choice, it could go for a carpet. It's much better for acoustics than obviously a really rigid hardwood floor or concrete slab. Yeah. It's an important thing to consider depending on what class of building you're looking at. This image here is from 25 King, which is a 10 story post and beam office project up in Brisbane, all built out of glulam and CLT, as you can see here. There's some LVL in there as well, I should say.
In office buildings or class five buildings, there isn't a requirement for airborne separation between levels, just because I suppose you might have multiple tenancies and it's a flexible arrangement. Still, we typically find to achieve a really nice positive outcome for everyone, including the tenants, it's really an effective solution to batten the floor and essentially just have a raised floor. It also means that you can actually design your systems, and for your tenants, it's an easy way to reticulate the systems through the building. In a multi residential situation, well, obviously there's much more stringent requirements for acoustics, and we typically see that there's a bit more attention that has to be paid. It's typically a build up on top of the floor, and sometimes it's a small build up underneath as well, as we can see in the graphics on the right hand side here.
Now, both of these graphics, really important to note, both of these graphics have two, or they have a pink layer underneath the floor, and that's the fire protective lining, whether that's a blaster board or a pro mat or some other product, it requires a fire protective lining or a deem to satisfy solution, as we'll see in a second. Now, looking at wall systems, we can see here, we've got the timber solution on the right. There's a steel frame solution on the left, which you might typically see in a concrete post and slab building, which we do obviously see normally for a multi-res situation. You can see these systems are really delivering the same airborne outcome. There's no impact requirements for walls typically. There's a couple of circumstances where there are, but generally this is the important number when you're looking at your party walls.
Now, an interesting take away here is that where the steel frame system is 300 ml in thickness because it has to allow for the big chunky concrete column to go in the middle, the timber system on the right hand side is actually the structure as well, so that is the party wall and the load bearing element holding the project above up. You can see that system is around about 40 mm thinner than the concrete or the steel one. That might not have sounded like a lot, but when you're dealing with a project which has, say, 100 apartments, you could have hundreds of metres of this party wall, and over time, or over an area, that adds up to quite a bit of gross floor area, which is money, at the end of the day. It's just extra market revenue from nowhere, essentially, for the developer. Really interesting outcome there.
From a fire point of view, there's two different ways we can go down when we're talking about fire. This is the deem to satisfy solution, which of course was brought into the NCC in 2016. It has four main requirements. The first one on the left hand side, you can see, is that all structural timber must be encapsulated by the required fire protective linings to reach the FRL for that element. So, that's that pink layer that I was showing, and the acoustic one, so you can see that's all fire red plaster board. Same here. That's all that pink layer. If you want to comply with a deem to satisfy solution, you must have this. You can't have pretty exposed columns and pretty beams and pretty CLT panels, but obviously this does work very well when you're doing a stud frame building. So, this is a really great solution for stud framing.
The other three requirements are that you must have sprinklers in your project, which of course is a requirement of mid-rise construction anyway these days. Any insulation in a structural cavity has to be non-combustible, which makes sense, and you need to use cavity barriers where they're required under the design. That's typically where there's an opportunity for fire spread between sole occupancy units and you need to maintain there is a cavity there for some reason, a cavity barrier is required to obviously stop the flame from getting through. That's the deem to satisfy. If we go down the other option, which we call the performance solution, or it used to be called the alternative solution, we can look at it in a slightly different way. If we want to break any of those rules, so if we want to expose the structural timber, this is what we'd be looking at.
Typically, this performance solution brings a fire engineer onto the project, and they'll obviously produce a fire engineering report, which is specific to the design of a project. As part of that report, they'll utilise what's known as there charring rate of the timber element, which essentially is just really a natural insulation phenomenon which happens when large pieces of timber are exposed to flame. So, I'm sure everyone has experienced it before, but if you have an open fire at home or if you've ever been camping and you've thrown a log on the fire, if it's a very big log, it might character a little bit on the outside, but there's a chance the fire will even just go out just because the log doesn't catch light very easily. It's the exact same concept with mass timber. Obviously we're talking about different species and all those different things, but the fundamental concept of charring is the exact same system which we're talking about here.
The fire engineer will take that into account, and they may allow you to expose timber in your project, depending on the design and the risk of the project itself. Now, we have this really good... there's a great video on YouTube, actually, which is prepared by Fire Engineering. I think it's actually their UK office. This really explains the charring phenomenon really, really well, I think. I've got a link to it in the presentation, obviously. We'll have this up on our website in the next couple of weeks, but also I recommend you just Google char rates, just char rates should do the job. I'm sure it'll come up.
Let's talk about substructure. This is really a no brainer. You know? It's pretty straight forward. If we're building a building out of concrete, we know concrete weighs about two and a half tonnes per cubic metre, or 2.4 tonnes. Your average timber species or soft wood timber species weighs about 500 kilos per cube. That's about a fifth of the weight of concrete. Obviously that means we're going to have lighter buildings, and lighter buildings typically require smaller footings or maybe fewer piles, and that could have a really significant impact on the costs of the project, particularly when you're building with contaminated soils or if you wanted to build over an existing project in a vertical extension, the light weight of the timber option can really have that good value. So, it's something that you should really be checking for. If you have two designs and the timber option has the same footings, then there's a question mark there because it should be smaller.
This is actually a good example of that, where we were looking at a case study again with Rider Levett Bucknall, Beck Property Group and Pro Build. We looked at this existing concrete building, which we redesigned in timber again, and we found the basement columns typically were about 25% smaller with the timber building. That's obviously the columns, but then also the footings as well, and 25% of those costs is a lot of money and a lot of time and excavation and installation. It's well worth keeping in mind. The next section is prelims, and this talks about, of course, preliminaries, the programme, and the labour. We'll go through it relatively quickly because it's a very big topic, of course, and we'll come back to it in more detail in another seminar at a later date.
Typically what we find are the main impacts on your preliminary costs are the shorter program, reduce listing requirements, smaller workforces on site, a safer site, and less tipping and less waste in general. Let's have a look at those. We typically find timber projects because they are prefabricated, typically, in a warehouse environment. The installation process on site is an installation process. It's assembly. It's not construction, it's just assembly. We typically find these projects do some in quite a bit faster than a comparison in situ concrete project. Here you can see this is from our tech design guide 26, I think. The timber option came in about 30% faster, and that's quite common. We've seen that quite a bit in the industry.
Looking at the cranage, we already know that thee timber solutions are lighter than the reinforced concrete solutions, so it makes sense that we might be looking at reduced cranage just because our panels are going to be lighter and our elements are going to be lighter. If we say our maximum panel weight is typically around about two tonnes, it might get a little bit higher than that, but normally that's the maximum weight. Throwing a heavy tower crane, a Favco 380D, like a big, expensive tower crane isn't really necessary unless you have access requirements or if you want to lift multiple panels at a time, it's using cricket bat to kill a fly, essentially, when you could be looking at a small tower or even mobiles, depending on your access to the site, or even, and this is quite common in Europe and even in the US these days, self erecting cranes. We don't really see these in Australia yet, but I think in a number of years as timber construction continues to increase in popularity, we'll see a number of these popping up around our middle suburbs.
A good example is built in Melbourne's north. It's a five story stud frame multi-residential project. You can see right here, that's a crane, a mobile crane, which is just picking up the floor element and dropping it on site. This is, as I said, a stud frame, so it's a lightweight solution, and that's actually a floor cassette, which is being picked up by the crane. With those floor cassettes, they can install a very large area per day. Moving on from there, we typically find that... and this is from our database and from our experience as well, a team will normally install about 94 square metres of project per day. Of course, that'll vary depending on the complexity of the design and other sort of specific factors of the project, but we can typically say at a high level pass on a project, we can be looking at about 94 square metres. That includes everything on it.
So, if you have, say, a post and beam floor plan and say it's 1,000 square metres over five floors, we know that's going to take about 12 days to build because it's about 1,000 square metres. If it's a panelised multi-res project like this one in the photo, which again was a great mid-rise stud frame project in Melbourne, again, we just apply that rate, about 94 square metres per day, and we can obviously calculate a really high level programme. The really interesting thing here of course as well is that the crew to install these elements is quite small. It's obvious that these structural systems see the crane time as a critical path, so obviously the more cranes, or you can only go as fast as the crane can lift, essentially. But by that token, you only need enough people to service the crane that you have on the project. All the structural work, I suppose, is kind of being done off site. This is just an installation process. You'll typically find six to eight people working on site during the structural phase, which is quite incredible when you compare it to other projects.
Another good example, this is a beautiful, beautiful project in the UK, quite a large floor area, as you can see, big spans, big high open areas. You'd think that this would require more people and more plants and equipment, but it took six workers I think it was 10 weeks, 12 weeks to install. It's a really impressive outcome. From a safety point of view, obviously safety is number one on every construction site around the world, hopefully, but particularly in Australia. No one really likes to think about it, but there is also a cost side to it, and I'm not talking about the cost of doing things safely, I'm talking about the cost of having someone injured on your site. If you have an LTI or a lost time injury, there is a number of unforeseen, unexpected costs, which are related with that, which may be making good whatever's been damaged when that injury has occurred, training someone to do that job, obviously paying medical expenses, and all these things add up to be quite a lot.
This is actually a great case study which is done by Work Safe in Queensland a couple years ago, looking at the impact of a lost time injury on a lower back injury for a worker who was obviously jack hammering. They found about $8,000 of direct cost to the building owner, sorry, to the business owner. But what's really interesting is that took almost five days you can see here, or about $54,000 in revenue to make that money back in profit. It's not just a... of course no one wants to tap in any way from a safety point of view and just from an empathetic point of view, but there is also a significant cost attached to it. Why is that important? Well, so, timber. Timber, as we have found and as Lendlease have found on their projects is incredibly safe to install. On all their projects in Australia so far, at least the last update, Lendlease haven't actually experienced a lost time injury in the installation of the structure, which is incredible. I challenge anyone to find a project of this scale where there hasn't been an LTI which isn't timber.
From a waste point of view, of course this is pretty logical, but if we're producing most of our structural elements off site in a factory, and the on site process is simply installation, we should have pretty small amounts of waste actually being generated in a structural base on site. Here's a couple of stats which you might find of interest. Murray Grove, one of really the first mid-rise projects in timber from around the world, generated a pile of dust every week. Now, I challenge that a little bit. I expect they probably had some packaging as well, but certainly with this amount of waste, they would have been looking at filling a skip every couple weeks maybe with their construction process. This has been continued on sites locally as well. It's not just a one off project thing. We really need to reassess our tipping cost when we're looking at timber projects.
This is also really important when we consider the actual cost of tipping waste in Australia. You can see here, this is a nice chart which charts the growth of landfill levies in various states over the last couple years, and I think we can all agree there's a pretty steady trend here where those numbers are going up. I think we understand logically that they're going to go up over time anyway, and much more than CLI, so if we can produce less waste in our construction, obviously from a sustainability point of view it's better, but we also have the financial incentive now as well. That's the estimating section. We're just going to have a very quick look at the system. I think we've got one slide here. This is really what everything is summarised down to, and everything really needs to be remembered when you're looking at estimating a project.
You need to remember that it's going to come in faster more often than not. Not every project will be faster depending on its design, depending on its location, but typically we do find these projects do come in a bit faster than the comparable project. Your prelims are typically reduced, of course, once again, subject to your design, but we do typically see reduced prelims in these mid-rise projects, and your footings, this is a no doubt one, will absolutely be smaller. Unless you're, I don't know, covering all your timber floors with a 120 ml slab of concrete, I think we can all agree that the timber solution will always be lighter and will always have those benefits of being able to build as a vertical extension or on those contaminated sites for less.
So, in conclusion, I'd like to take a second just to plug our services. Of course we do completely free advice and support to project teams, anyone who's interested in building or designing or being involved in a mid-rise timber project, our team is really here for you. We're independent, we're completely impartial. We just want to see a successful project, because of course that will lead to more projects in the future. I recommend getting in touch if you do have a question. Finally, of course, all of our resources are independently and free to use. You have to consider your prelim costs where these timber projects are typically faster and safer and less disruptive and [inaudible 00:53:49]. That's me. Thank you very much and feel free to take a screenshot of my details or give us a call or send me an email at any time.
Thank you very much for that, Laurence. That was great. I'm going to now move to the Q&A section, so I'll just remind everybody you can leave your questions in the Q&A sections in the Zoom. There's a few coming through chat as well, so that's great. I'd like to introduce Paolo Lavisci to the panel. Paolo's extensive experience in developing and using wood products encompasses advisory and hands on roles in their design and construction of timber structures, project management, research, product development, teaching and training. With a PhD in industrial technologies, wood, Paulo worked in the plywood industry for seven years before starting a wood engineering practise through machine coordinated design and delivery of multi-story timber buildings, before joining the WoodSolutions mid-rise advisory programme in 2016. Welcome, Paolo. How are you?
Paolo Lavisci: Perfect, and what about you and all the attendees?
Going very well.
Paolo Lavisci: Yeah.
There's 200 right now, so there's a few interesting questions that are coming through, Paulo. I'd like to start with a question directed at you, Paulo. What are some of the limitations in pre fabrication and timber construction in context to what Laurence has been speaking about?
Paolo Lavisci: Yes. In terms of limitations, I would say mostly timber is not able to be used in ground contact, in direct ground contact without preservatives. But for mid-rise construction, it's certainly not advisable to think about wood based foundations, so similar. The first slab should be off the ground, and typically people design for a concrete structure up to level one, incorporating also whatever goes into the ground level, pictures and services and plans and everything, and this allows timber to stay off the ground for both termite and moisture related, fungi related durability.
Paolo Lavisci: Then off the ground, there's no difficulty to design with good detailing for durability for all this type of logical risks. Our guide number five illustrates the principle of designing for durability with timber quite well. Then another limitation can be the height. Currently there are projects up to 18, 20 stories, which have been built or are being built in timber. Skidmore, Owings & Merrill, a top engineering firm specialising in high rises, they did a full design of a 40 story building, a redesign, actually of one of their most successful designs in concrete for this durability. In timber, they demonstrated visibility, full visibility.
Paolo Lavisci: Then, of course, if we are thinking about what is possible in terms of [inaudible 00:57:11], for instance, with steel construction, then it's difficult to do the same, exactly the same with timber. I'm not saying it's impossible, but it will lead to very heavy dimensions, so it's not meaningful to imitate what you can do with other materials with timber. You need to design for timber and make the most of this wonderful and efficient material. Basically that's it, but on the other hand, timber based design is much better on the difficult sites, as Laurence described so far.
Thanks for that, Paulo. Laurence, you can see the Q&A coming through at the moment?
Yep.
Might just let you choose the questions that you might like to answer, and Paulo, you might like to join in.
Yep, yep. Look, there's a couple which I think are important to cover up on just quickly just to make sure that everyone is clear on a couple of things in the presentation. There's a question from Chris asking if we can explain what prelim costs are. I'm sorry, I should have discussed this just quickly or introduced it quickly. Preliminary costs are essentially the costs involved in delivering a construction project which aren't specifically the materials and things going into the building. Obviously if we're building an eight story timber building, the timber which is going in isn't a prelim cost, but things like, say, gantry hire or supervision or permits or all of those, shed hire, toilet hire, temporary services, all of that falls under the prelim costs banner.
Of course you can imagine they're all very time sensitive, so if we can bring the project in faster, you have to pay less, essentially, which is a good outcome. The other one which I just wanted to clarify was that from Charles, who's asking if six to eight people to install 94 square metres per day includes the installation of vertical elements. Yes, basically. That includes everything which is on top of the floor element as well, so your low bearing system. Now that they're out of the way, let's see what else there is.
Paolo Lavisci: Nikolai has a question about the delivery times. They are comparable. Not exactly the same, they may not be the same, but these will vary with the level of supply that the same company is engaged with in a certain moment. When they are a bit low in their orders, they may be faster. When they are a bit more... how can I say, busy, they may take a little longer, both locally or from overseas. Otherwise they may be comparable, yes.
Yeah.
Paolo Lavisci: Then another interesting question, which I think, Adam, you will be more indicated than us to answer this from this anonymous about what will be an ideal set of geometries and all alignment, et cetera, for a timber structure.
Thank you, Paolo. Who read that question? I'll be able to answer it. I can't find it, actually.
Paolo Lavisci: Number 48 again from anonymous.
Okay. That's a great question because this is one of the most important things to get a successful timber project, because like Laurence said, it can come in cost competitive or less than concrete if designed from what we call a timber first paradigm, so designing the material in mind. For residential, we recommend spans that are under six metres. So, you open yourself up to a wide range of products, and the floor structure decks are similar to that of concrete, they're very competitive. So, when you push past six metres, a little bit more difficult. Office buildings, a little bit different. We can get the nine metre spans that you're looking for in office grids in a primary direction and secondary direction, actually. Regarding wall alignments, avoid them at all costs, especially on lower levels. The upper levels, you might be able to get away with minor load transfer, but you do get punished more in these buildings than you would for traditional infrastructure.
Paolo Lavisci: Then I will ask everybody to have a look at the last two questions. The second last from Liz is about any project currently designed in Queensland, yes, there is a few project. One of them is actually under construction, which is a very interesting one that you could follow. We have our colleague, Ben Ashtal in Brisbane, so we can contact Ben and go and have a look together as soon as the possibility to go around and be open again, but the building site is open. Then the last question that I see from Nick Mirestone, oh, probably not the last one, Nick Mirestone, a good friend of ours and now the CLT director at Catella, so congratulations, Nick. We will be very, very happy to do a cost engineering guide for hybrid construction if you join us as consultant because you are one of the most experts in the world of this.
Paolo Lavisci: Then Joseph Evio, how does traditional developer approach this? That's an interesting question. Traditional developers, of course, they look at two things, whether it can cost less than mid [inaudible 01:03:12], which goes into the safety, and whether their clients will appreciate better a timber based construction. Normally they find positive answers to both. Some of them have tested the market, actually, they have tried to promote it as a timber building and found some positive feedback from their clients or tenants, and that follow up, this is why they decided they are not charities, so they do it. If they choose timber, they choose it for some good reasons.
Thank you, Paolo and Laurence. We're probably going to take one more question. I might let you, Laurence, choose a question as a final one and we might pick one-
On the spot. Probably... oh, that's already been answered.
You can name a few if you like, Laurence, and then you choose, if you like.
Yeah, okay. Look, I think Mark has an interesting one on penetrations in the lower stories of a building, how different that is. I mean, look, I'll talk about it from a cost perspective and then maybe, Adam, you might want to touch on it from a structural point of view. Obviously if we're building big buildings, loads on the lower floors can be significant depending on the structural system that you're using and the design, of course. From a cost point of view, if you need penetrations at lower levels, even if it's a variation, penetration, timber is certainly a much, much better solution than you would find in concrete, just from personal experience.
Coring through concrete as a variation can be a slow, noisy, disruptive, expensive process, whereas if we're going through timber, we all know how you can cut through a piece of timber pretty easily. It can take, depending on the size of the element, it can be a bit of an operation, but it is still much faster and safer and quieter, and we are the concrete alternative. Would you like to maybe touch on penetrations, Adam?
I think you covered it pretty well, Laurence. Penetrations with timber, it's like all structural materials. You just need to work out the load transfer, and in that section you take away whatever's taken out. So, engineering in generally with timber, it's just structural engineering fundamentals that are similar to concrete, and penetrations is no different.
Paolo Lavisci
There's a good number of other very good questions. Shall we go on? We can certainly answer these questions individually to email.
Yeah.
Paolo Lavisci: So, Adam, what do you suggest?
I suggest if anyone's got any burning questions, feel free to leave it as an email to us, so you can go jones@woodsolutions.com.au, and I'll pass it onto Laurence or Paolo, or I'll answer it myself. So, feel free to get in touch with us. I might leave it there for yourself, Laurence and Paulo, so thank you very much for the presentation and the Q&A.
Paolo Lavisci: Thank you, guys, for joining us.
Thank you.
Okay. So, just before everyone goes, I'd like to remind everyone of next week's webinar. Again, it's going to be at 11:00 AM. We've got Richard Maddock, who's the associate of the specialist modelling group at Fosters & Partners talking about parametric design, design optimisation, and how it relates to pre fabrication and artificial intelligence, even. This guy has done some extremely interesting projects. As I said at the start, I had an interesting with him on the Timber Talks podcast recently which was released last week. So, there has been a launch for season three of the Timber Talks podcast, so if you haven't listened to this yet, I highly recommend that you subscribe. So, it's something you can listen to when you're taking the dog for a walk or going to the gym, which is probably difficult now, but gym in your home gym or any moments like that.
We've got Steven Mitchell talking about sustainability, Richard Maddock, as I said, and James Fitzpatrick, who's the architect for the award winning Seed House project in New South Wales. As a reminder with CPD, I'll be sending you a link to a SurveyMonkey that will have the three questions that are related to this webinar, and you'll be able to fill out the form yourself, and then this will qualify as formal CPD. As a note for future webinars there, you need to attend the live webinar to be able to be eligible for the formal CPD component. Again, thank you very much, everybody, for your time in attending this morning. I hope you got a lot of value out of this presentation, and I look forward to seeing you in next week's webinar with Richard Maddock on design optimisation using parametric design. Thank you very much.
Paolo Lavisci: Thank you, Adam.